Isothermal forging method of straight bevel gear
A straight bevel gear and isothermal forging technology, applied in the field of warm forging, can solve the problems of gear bending strength, contact fatigue strength reduction, incomplete filling of tooth shape, difficulty in adjusting machine tools, etc. The effect of small quantity and lower production cost
- Summary
- Abstract
- Description
- Claims
- Application Information
AI Technical Summary
Problems solved by technology
Method used
Image
Examples
Embodiment 1
[0036] like figure 1 Shown, the method for the isothermal forging of straight bevel gear of the present invention comprises the following steps:
[0037] The first step: the calculation and blanking of the blank. According to the bevel gear forging diagram, combined with the theory of constant volume, the blank size is calculated. The shearing machine is used to blank the bar steel, and then the oxide skin on the surface of the bar is taken out, the outer surface is turned and chamfered to obtain the required shape and size of the blank.
[0038] The second step: mold heating and blank heating and lubrication. The heating device of the mold adopts a resistance wire ceramic heating ring, such as image 3 Shown is a hollow ceramic cylinder 7 with resistance wires 6 wound in the two walls. The heating method of the billet is induction heating by medium frequency induction furnace. First preheat the billet to 80-120°C, spray commercial water-based graphite lubricant, and then...
Embodiment 2
[0046]This embodiment is the same as Embodiment 1, the difference is that in the third step of the isothermal forging forming process, the toothed die 1 goes down at a speed of 0.08mm / s to upset the blank 4, when the back cone die 2 and the toothed After the mold 1 is closed, the upper punch 3 and the lower punch 5 relatively extrude the billet at the same speed of 0.08mm / s to fill the mold cavity and form a punching skin with a certain thickness. After the forming is completed, the mold is demoulded .
Embodiment 3
[0048] This embodiment is the same as Embodiment 1, except that in the third step of the isothermal forging forming process, the toothed die 1 descends at a speed of 0.03mm / s to upset the blank 4, when the back cone die 2 and the toothed After the mold 1 is closed, the upper punch 3 and the lower punch 5 relatively extrude the billet at the same speed of 0.03mm / s to fill the mold cavity and form a punching skin with a certain thickness. After the forming is completed, the mold is demoulded .
PUM
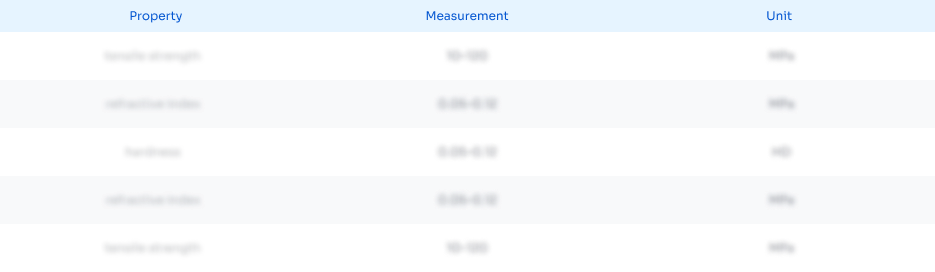
Abstract
Description
Claims
Application Information

- R&D
- Intellectual Property
- Life Sciences
- Materials
- Tech Scout
- Unparalleled Data Quality
- Higher Quality Content
- 60% Fewer Hallucinations
Browse by: Latest US Patents, China's latest patents, Technical Efficacy Thesaurus, Application Domain, Technology Topic, Popular Technical Reports.
© 2025 PatSnap. All rights reserved.Legal|Privacy policy|Modern Slavery Act Transparency Statement|Sitemap|About US| Contact US: help@patsnap.com