Medium diameter speaker diaphragm bonding process
A speaker and sound film technology, which is applied in the field of medium-caliber speaker bonding sound film technology, can solve the problems of low operating efficiency, affecting the production cycle of the speaker, and waste of action, so as to improve operating efficiency, optimize the sound film bonding process, shorten the The effect of the production cycle
- Summary
- Abstract
- Description
- Claims
- Application Information
AI Technical Summary
Problems solved by technology
Method used
Examples
Embodiment 1
[0018] A kind of bonding sound film technology of medium-bore speaker, it comprises the following steps:
[0019] S1. The horn is buckled into the fixture, and the connection is firm;
[0020] S2. Speaker surface treatment: remove oil or dust on the surface of the speaker to ensure that there is no debris on the surface of the speaker;
[0021] S3. Glue injection: inject sound film glue on the surface of the speaker, the thickness of the glue is even and in place, and there is no bonding blind spot;
[0022] S4. Positioning: attach the sound film to the glue injection surface of the speaker, and the attaching time is 20 minutes;
[0023] S5. Inserting the pressure column: slowly insert the pressure column from the bottom of the fixture. The clamp has a through hole, and the axial distance between the through hole and the pressure column does not exceed 0.02mm;
[0024] S6. Sound pressure film: continue to insert the pressure column until the pressure column touches the sound...
Embodiment 2
[0027] A kind of bonding sound film technology of medium-bore speaker, it comprises the following steps:
[0028] S1. The horn is buckled into the fixture, and the connection is firm;
[0029] S2. Speaker surface treatment: remove oil or dust on the surface of the speaker to ensure that there is no debris on the surface of the speaker;
[0030] S3. Glue injection: inject sound film glue on the surface of the speaker, the thickness of the glue is even and in place, and there is no bonding blind spot;
[0031] S4. Positioning: paste the sound film on the surface of the speaker with glue injection, and the bonding time is 15 minutes;
[0032] S5. Inserting the pressure column: slowly insert the pressure column from the bottom of the fixture. The clamp has a through hole, and the axial distance between the through hole and the pressure column does not exceed 0.02mm;
[0033] S6. Sound pressure film: continue to insert the pressure column until the pressure column touches the sou...
Embodiment 3
[0036] A kind of bonding sound film technology of medium-bore speaker, it comprises the following steps:
[0037] S1. The horn is buckled into the fixture, and the connection is firm;
[0038] S2. Speaker surface treatment: remove oil or dust on the surface of the speaker to ensure that there is no debris on the surface of the speaker;
[0039] S3. Glue injection: inject sound film glue on the surface of the speaker, the thickness of the glue is even and in place, and there is no bonding blind spot;
[0040] S4. Positioning: paste the sound film on the surface of the speaker with glue injection, and the bonding time is 30 minutes;
[0041] S5. Inserting the pressure column: slowly insert the pressure column from the bottom of the fixture. The clamp has a through hole, and the axial distance between the through hole and the pressure column does not exceed 0.02mm;
[0042] S6. Sound pressure film: continue to insert the pressure column until the pressure column touches the sou...
PUM
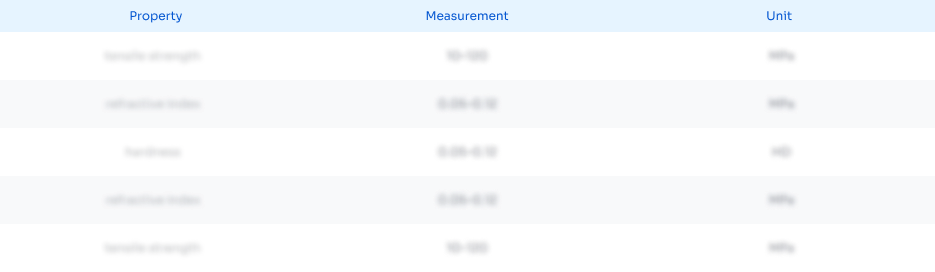
Abstract
Description
Claims
Application Information

- R&D Engineer
- R&D Manager
- IP Professional
- Industry Leading Data Capabilities
- Powerful AI technology
- Patent DNA Extraction
Browse by: Latest US Patents, China's latest patents, Technical Efficacy Thesaurus, Application Domain, Technology Topic, Popular Technical Reports.
© 2024 PatSnap. All rights reserved.Legal|Privacy policy|Modern Slavery Act Transparency Statement|Sitemap|About US| Contact US: help@patsnap.com