Fiber reinforced composite/metal lamination complete cycle instantaneous drilling axial force prediction method
A composite material and metal lamination technology, applied in the field of mechanical processing, can solve the problems of losing instantaneous fluctuation information and affecting the decision-making of lamination material drilling process parameters, etc.
- Summary
- Abstract
- Description
- Claims
- Application Information
AI Technical Summary
Problems solved by technology
Method used
Image
Examples
Embodiment Construction
[0061] The present invention will be further described below in conjunction with accompanying drawings and examples.
[0062] Such as Figure 1-3 shown.
[0063] A method for predicting the axial force of fiber-reinforced composite material / metal laminated full-cycle instantaneous drilling, which includes the following steps:
[0064] First, get the primary parameters. CFRP layup sequence is [0° / -45° / 90° / 45°] 5S , the thickness of each layer is 0.125mm, the total thickness is 5mm, the longitudinal Young's modulus is 140GPa, the transverse Young's modulus is 8.5GPa, and Poisson's ratio is 0.34; the thickness of aluminum alloy is 5mm, the Young's modulus is 70GPa, and Poisson's ratio is 0.34; Diameter 3.5mm, front angle 118°, nominal helix angle 30°, static reference relief angle 12°, chisel edge width 0.7mm, chisel edge bevel angle 126°; spindle speed 4000r / min, feed 0.06mm / s. The main cutting edge and chisel edge of the twist drill are divided into infinitely small micro-e...
PUM
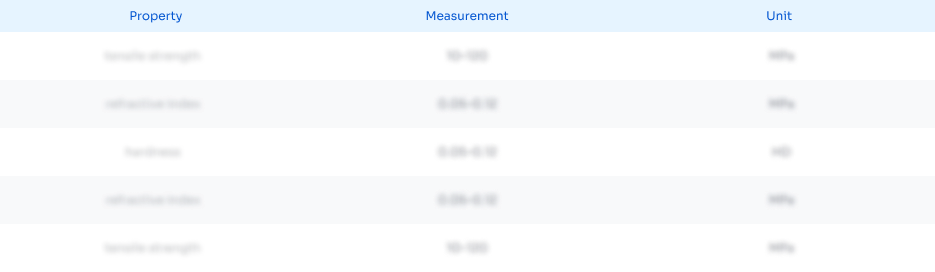
Abstract
Description
Claims
Application Information

- R&D Engineer
- R&D Manager
- IP Professional
- Industry Leading Data Capabilities
- Powerful AI technology
- Patent DNA Extraction
Browse by: Latest US Patents, China's latest patents, Technical Efficacy Thesaurus, Application Domain, Technology Topic, Popular Technical Reports.
© 2024 PatSnap. All rights reserved.Legal|Privacy policy|Modern Slavery Act Transparency Statement|Sitemap|About US| Contact US: help@patsnap.com