Trifluoromethanesulfinate purification method
A technology of trifluoromethyl sulfinic acid and sodium trifluoromethyl sulfinate, which is applied in the field of purification of trifluoromethyl sulfinic acid, can solve the problem of not being suitable for large-scale promotion and use, complex preparation process, and many inorganic salts. and other problems, to achieve the effect of low cost of purification equipment and purified raw materials, simple preparation process and simple operation method
- Summary
- Abstract
- Description
- Claims
- Application Information
AI Technical Summary
Problems solved by technology
Method used
Examples
Embodiment 1
[0038] In a 2000ml three-necked flask equipped with a stirrer, add 300g of 60-70% sodium trifluoromethanesulfinate industrial product, 20g of anhydrous magnesium sulfate, 500g of ethyl acetate solvent, and stir at 20-30°C for 0.5h, Stop stirring, filter the discharge, collect the filtrate, put the filter cake back into the flask, add 500g of ethyl acetate solvent to the flask, stir at 20-30°C for 0.5h, stop stirring, filter the discharge, collect the filtrate, and filter the cake Then put it back into the flask, add 300g ethyl acetate solvent, stir at 20-30°C for 0.5h, stop stirring, filter the discharge, collect the filtrate, rinse the filter cake with a small amount of ethyl acetate solvent, remove the filter cake , collect three filtrates and the filtrate solution of rinsing, evaporate to dryness with rotary evaporator under negative pressure, reclaim ethyl acetate solvent, recycle, add 1000g deionized water in the kettle, dissolve sodium trifluoromethyl sulfinate solid, An...
Embodiment 2
[0041] In a 2000ml three-necked flask equipped with a stirrer, add 300g of 60-70% sodium trifluoromethanesulfinate industrial product, 20g of anhydrous magnesium sulfate, 500g of acetonitrile solvent, stir at 20-30°C for 0.5h, stop stirring , filter the output, collect the filtrate, put the filter cake back into the flask, add 500g of acetonitrile solvent to the flask, stir at 20-30°C for 0.5h, stop stirring, filter the output, collect the filtrate, and put the filter cake back into the Add 300g of acetonitrile solvent to the flask, stir at 20-30°C for 0.5h, stop stirring, filter the discharge, collect the filtrate, rinse the filter cake with a small amount of acetonitrile solvent, remove the filter cake, collect the filtrate three times and rinse The filtrate solution was evaporated to dryness with a rotary evaporator under negative pressure, and the acetonitrile solvent was recovered for recycling. 1000g of deionized water was added to the kettle to dissolve the sodium triflu...
Embodiment 3
[0043] In a 2L reaction kettle, add 300kg of 60-70% sodium trifluoromethanesulfinate industrial product, 20kg of anhydrous magnesium sulfate, 500kg of ethyl acetate solvent, stir at 20-30°C for 0.5h, stop stirring, and discharge Filtrate, collect the filtrate, put the filter cake back into the flask, add 500kg ethyl acetate solvent to the flask, stir at 20-30°C for 0.5h, stop stirring, filter the discharge, collect the filtrate, and put the filter cake back into the flask Add 300kg of ethyl acetate solvent to the flask, stir at 20-30°C for 0.5h, stop stirring, filter the discharge, collect the filtrate, rinse the filter cake with a small amount of ethyl acetate solvent, remove the filter cake, collect and filter three times liquid and rinsed filtrate solution in the reaction kettle, evaporated to dryness under reduced pressure, reclaim the solvent ethyl acetate, and recycle, add 1000kg deionized water to the kettle, dissolve the sodium trifluoromethylsulfinate solid to obtain t...
PUM
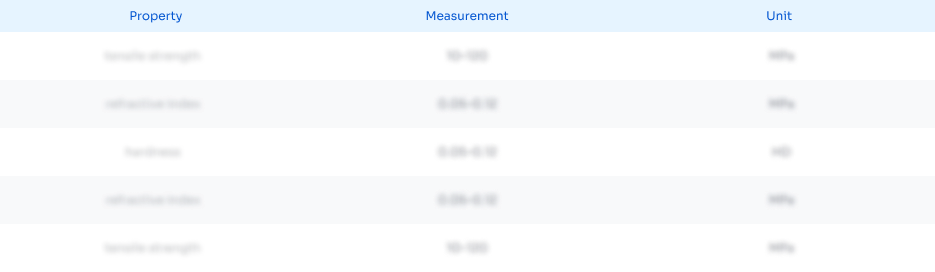
Abstract
Description
Claims
Application Information

- R&D
- Intellectual Property
- Life Sciences
- Materials
- Tech Scout
- Unparalleled Data Quality
- Higher Quality Content
- 60% Fewer Hallucinations
Browse by: Latest US Patents, China's latest patents, Technical Efficacy Thesaurus, Application Domain, Technology Topic, Popular Technical Reports.
© 2025 PatSnap. All rights reserved.Legal|Privacy policy|Modern Slavery Act Transparency Statement|Sitemap|About US| Contact US: help@patsnap.com