Non-support three-dimensional printing method based on inclined layering
A 3D printing, support-free technology, applied in the direction of additive processing, etc., can solve the problems of poor surface quality between supports and entities, waste of printing materials, long post-processing time, etc., to save printing raw materials, improve printing efficiency, save Effect of the process of support removal
- Summary
- Abstract
- Description
- Claims
- Application Information
AI Technical Summary
Problems solved by technology
Method used
Image
Examples
Embodiment 1
[0082] Here, a shell part generated by 3D design software is taken as an example to illustrate the trajectory code processing process and the final algorithm execution effect of the present invention.
[0083] Such as Figure 8 As shown, the model has common design elements such as plane features, hole features, and shell features. Its size is 80mm*80mm*80mm. In order to demonstrate the actual oblique slicing principle and visualization effect of the present invention, Figure 8 The layer height in is set to 5 times (0.5mm ~ 1.5mm) in the actual algorithm. It can be clearly seen from the figure that the printed model is discretized into slices layer by layer, and the model is divided into three parts in total, using horizontal codes and inclined motion codes respectively, and the two parts are oblique layered structure slice inclination angle and layer height There are also differences. By calculation, the inclination angles of slices are 55 degrees and 74 degrees respectiv...
Embodiment 2
[0085] Here, a common complex kettle model is taken as an example to illustrate the effect of the oblique slice trajectory of the present invention when dealing with complex surfaces.
[0086] Such as Figure 9 As shown in the model display, the method of magnifying the layer height to 5 times is also used to obtain a better visualization effect. The model can be roughly divided into four regions after surface identification. Among them, areas 1, 3, and 4 whose inclination angles are less than 60 degrees are all marked as non-overhanging structures, and can directly use horizontal slices to obtain processing tracks, while area 2 has a relatively large overhanging surface, so the inclination in the present invention is adopted slice method. Area 1, Area 3, and Area 4 all use a layer height of 0.2mm, and the printing speed and filling rate are the same as in Example 1. Area 2 is used as the processing section of inclined layering, with a layer height of 0.1 mm and a slice ang...
Embodiment 3
[0088] Here, a typical cantilever beam model is taken as an example to illustrate the processing effect of the inclined slice trajectory of the present invention on the limit overhang structure.
[0089] Such as Figure 10 As shown, the cantilever beam model includes three parts: the base for bonding the upper structure with the printer platform, the vertical beam and the suspension beam. The triangular base is designed with a larger area, mainly to improve the adhesion between the model and the printer platform, and to counteract the overturning moment during the printing process. The main structure of the cantilever beam shown in area 3 is in a horizontal state and is in the limit printing position with an inclination angle of 90 degrees. When there is no support structure, due to the effect of gravity, the accumulation of materials cannot be achieved by horizontal layering. The slicing result shown in the figure is similar to that of Example 1, consisting of multiple obliq...
PUM
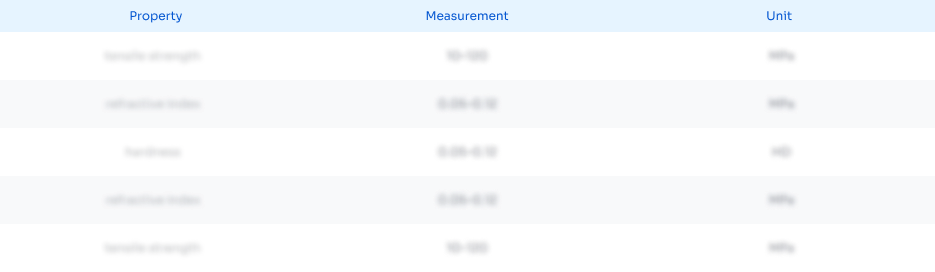
Abstract
Description
Claims
Application Information

- R&D
- Intellectual Property
- Life Sciences
- Materials
- Tech Scout
- Unparalleled Data Quality
- Higher Quality Content
- 60% Fewer Hallucinations
Browse by: Latest US Patents, China's latest patents, Technical Efficacy Thesaurus, Application Domain, Technology Topic, Popular Technical Reports.
© 2025 PatSnap. All rights reserved.Legal|Privacy policy|Modern Slavery Act Transparency Statement|Sitemap|About US| Contact US: help@patsnap.com