AGV device capable of achieving automatic stacking
A stacking and main gear technology, applied in the field of AGV devices, can solve the problems of incapable of carrying large-capacity storage of goods, inability to solve the closed-loop control of manipulators, and complex structures, so as to improve automation level and production efficiency, and improve long-distance transportation of materials Inconvenience, complexity reduction effect
- Summary
- Abstract
- Description
- Claims
- Application Information
AI Technical Summary
Problems solved by technology
Method used
Image
Examples
Embodiment 1
[0036] Such as figure 1 As shown, the present embodiment includes: a stacking mechanical arm mechanism 4, a rotating platform mechanism 2, an AGV two-wheel drive chassis 1, a loading platform 3 and a lifting platform mechanism 28 arranged on the AGV two-wheel drive chassis 1, wherein: the rotation The platform mechanism 2 is arranged above the lifting platform mechanism 28 , and the palletizing mechanical arm mechanism 4 is arranged above the rotating platform mechanism 2 .
[0037] The AGV two-wheel drive chassis 1 includes: an acrylic base plate, two driving wheels and a universal wheel, wherein: the universal wheel is arranged on the front part of the acrylic base plate, and the two driving wheels are respectively arranged on the two rear parts of the acrylic base plate. side.
[0038] The two drive wheels are respectively driven by two DC motors with speed reducers to realize the two-wheel differential motion.
[0039] The rotating platform mechanism 2 includes: a rotati...
PUM
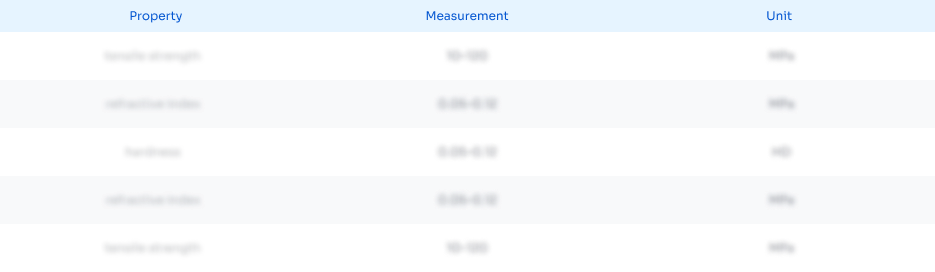
Abstract
Description
Claims
Application Information

- R&D
- Intellectual Property
- Life Sciences
- Materials
- Tech Scout
- Unparalleled Data Quality
- Higher Quality Content
- 60% Fewer Hallucinations
Browse by: Latest US Patents, China's latest patents, Technical Efficacy Thesaurus, Application Domain, Technology Topic, Popular Technical Reports.
© 2025 PatSnap. All rights reserved.Legal|Privacy policy|Modern Slavery Act Transparency Statement|Sitemap|About US| Contact US: help@patsnap.com