Method for eliminating color difference defects of special-effect color-coated sheets
A color-coated board and color difference technology, which is applied to the surface coating liquid device, coating, special surface, etc., can solve the problems of low product yield and restrict the stability of special-effect color-coated boards, so as to improve the product yield, The effect of reducing the cost of quality
- Summary
- Abstract
- Description
- Claims
- Application Information
AI Technical Summary
Problems solved by technology
Method used
Examples
Embodiment 1
[0027] 1. Paint processing and color confirmation
[0028] 1. When making paint, first do not add additives related to special effects. After mixing the resin, color paste and other additives, take the paint sample and stir it at high speed to measure the color difference, and control the color difference value △E to 0.7.
[0029] 2. After the color difference adjustment is qualified, add additives related to special effects, take the paint sample after high-speed stirring, scrape the sample and measure the color difference again, control the color difference value △E to 0.5, and the color difference items △L, △a, △b are respectively 0.2, 0.25, 0.3, and the scraped sample is basically consistent with the standard batch sample visually.
[0030] 3. Scrape samples in the laboratory to simulate the change trend of product color difference within the fluctuation range of normal process parameters, and establish a trend chart to determine the direction and range of process adjustme...
Embodiment 2
[0045] 1. Paint processing and color confirmation
[0046] 1. When making paint, first do not add additives related to special effects. After mixing the resin, colorant and other additives, take the paint sample after high-speed stirring and scrape the sample to measure the color difference. The color difference value △E is controlled at 0.9.
[0047] 2. After the color difference adjustment is qualified, add additives related to special effects, take the paint sample and stir it at a high speed, scrape the sample and measure the color difference again, control the color difference value △E0.3, and the color difference sub-items △L, △a, △b are respectively 0.3, 0.26, 0.22, and visually compare the scraped sample with the standard batch sample, which is basically the same.
[0048] 3. Scrape samples in the laboratory to simulate the change trend of product color difference within the fluctuation range of normal process parameters, and establish a trend chart to determine the di...
PUM
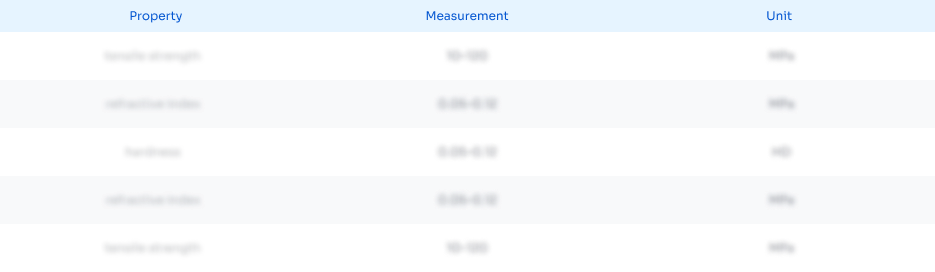
Abstract
Description
Claims
Application Information

- Generate Ideas
- Intellectual Property
- Life Sciences
- Materials
- Tech Scout
- Unparalleled Data Quality
- Higher Quality Content
- 60% Fewer Hallucinations
Browse by: Latest US Patents, China's latest patents, Technical Efficacy Thesaurus, Application Domain, Technology Topic, Popular Technical Reports.
© 2025 PatSnap. All rights reserved.Legal|Privacy policy|Modern Slavery Act Transparency Statement|Sitemap|About US| Contact US: help@patsnap.com