Single-layer prefabricated assembly type reinforced concrete beam-column joint
A reinforced concrete and prefabricated assembly technology, which is applied in the direction of architecture and building construction, can solve the problems of high installation and positioning accuracy, large amount of additional support, and difficulty in ensuring the integrity of beam-column joints.
- Summary
- Abstract
- Description
- Claims
- Application Information
AI Technical Summary
Problems solved by technology
Method used
Image
Examples
specific Embodiment approach 1
[0020] Specific implementation mode one: combine Figure 1 to Figure 11 Describe this embodiment, a single-layer prefabricated reinforced concrete beam-column node of this embodiment, which includes a vertical column section 1 and a plurality of node superimposed beam sections 2, the vertical column section 1 is a rectangular column section, and the vertical column section 1 is a rectangular column section. The straight column section 1 is divided into an upper column section and a lower column section. The column heights of the upper column section and the lower column section are respectively 1 / 2 of the storey height where they are located. Multiple node superimposed beam sections 2 are distributed in the rectangular column section. On the side, the lengths of multiple nodal superimposed beam sections 2 are 1 / 3 of the span of their respective beams, and the nodal superimposed beam sections 2 are integrated with the vertical column section 1, and each nodal superimposed beam s...
specific Embodiment approach 2
[0021] Specific implementation mode two: combination figure 1 To illustrate this embodiment, the trough-shaped pouring section 2-1 of each node superimposed beam section 2 of this embodiment also includes a floor support platform 2-1-1 and a beam section occlusal groove 2-1-2, and the floor support platform 2 -1-1 is used for the placement of laminated slabs, and the beam segment occlusal groove 2-1-2 is used for occlusal secondary pouring of concrete. The concrete poured for the second time of the beam section relies on the occlusal groove 2-1-2 of the beam section in the length direction, and relies on the inner wall of the floor support platform to resist the lateral slippage of the concrete in the occlusal groove 2-1-2 perpendicular to the length direction . The end of the trough-shaped pouring section 2-1 is in a triangular sawtooth shape. Other compositions and connections are the same as in the first embodiment.
specific Embodiment approach 3
[0022] Specific implementation mode three: combination figure 1 The present embodiment will be described. The meshing teeth of the present embodiment are triangular in shape. Such setting is convenient for realization. Other compositions and connections are the same as those in Embodiment 1 or Embodiment 2.
PUM
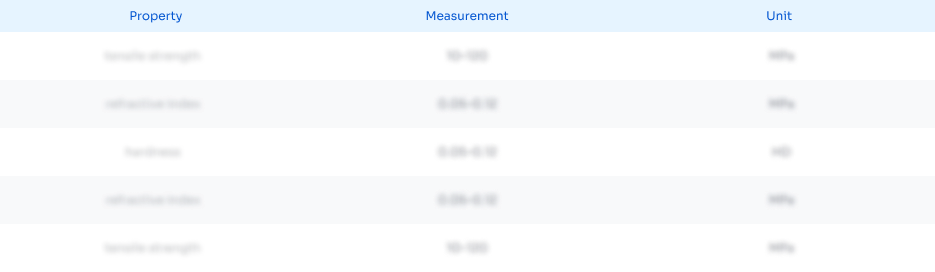
Abstract
Description
Claims
Application Information

- R&D
- Intellectual Property
- Life Sciences
- Materials
- Tech Scout
- Unparalleled Data Quality
- Higher Quality Content
- 60% Fewer Hallucinations
Browse by: Latest US Patents, China's latest patents, Technical Efficacy Thesaurus, Application Domain, Technology Topic, Popular Technical Reports.
© 2025 PatSnap. All rights reserved.Legal|Privacy policy|Modern Slavery Act Transparency Statement|Sitemap|About US| Contact US: help@patsnap.com