Multi-laser-head laser cutting machine
A laser cutting machine and multi-laser technology, applied in laser welding equipment, welding equipment, metal processing equipment, etc., can solve problems such as increased procurement, increased labor costs and material costs, and inability to complete complex forming and cutting requirements, so as to improve finished products Quality, the effect of reducing labor and material costs
- Summary
- Abstract
- Description
- Claims
- Application Information
AI Technical Summary
Problems solved by technology
Method used
Image
Examples
Embodiment 1
[0036] Such as figure 1 The mixed light source laser cutting machine shown includes a worktable 4, a number of waste discharging devices 5 are arranged at the lower part of the worktable, and a beam device 2 that moves back and forth relative to the worktable is installed above the worktable, and a laser tube is installed inside the beam device 2 3. The beam device 2 is also installed with a multi-laser head cutting assembly 1 that moves left and right relative to the beam device. The light beam emitted by the laser tube 3 is reflected by the reflection structure and transmitted to the multi-laser head cutting assembly 1, inside the multi-laser head cutting assembly 1. It includes a carbon dioxide laser device and at least one non-carbon dioxide laser laser device.
[0037] The laser tube emits a carbon dioxide laser radio frequency tube light source, and the non-carbon dioxide laser laser device is a fiber laser light source device.
[0038] Such as figure 2 As shown, the upper s...
Embodiment 2
[0048] A multi-laser laser cutting machine with the same structure as the multi-laser laser cutting machine in Example 1, wherein the laser tube emits a carbon dioxide laser radio frequency tube light source, and the non-carbon dioxide laser laser device is a solid-state (YAG) laser light source device.
Embodiment 3
[0050] The multi-laser-head laser cutting machine in embodiment 1 is a multi-laser-head laser cutting machine with the same structure, wherein the laser tube emits a carbon dioxide laser tube light source, and the non-carbon dioxide laser laser device is a semiconductor laser light source device.
PUM
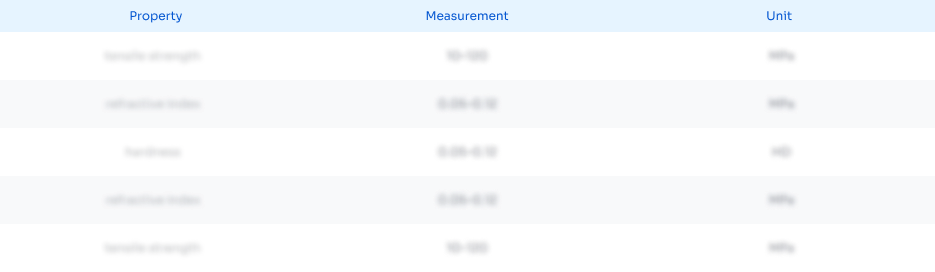
Abstract
Description
Claims
Application Information

- R&D
- Intellectual Property
- Life Sciences
- Materials
- Tech Scout
- Unparalleled Data Quality
- Higher Quality Content
- 60% Fewer Hallucinations
Browse by: Latest US Patents, China's latest patents, Technical Efficacy Thesaurus, Application Domain, Technology Topic, Popular Technical Reports.
© 2025 PatSnap. All rights reserved.Legal|Privacy policy|Modern Slavery Act Transparency Statement|Sitemap|About US| Contact US: help@patsnap.com