Control moment gyroscope framework control system and control moment gyroscope framework control method for restraining dynamic unbalance disturbance of rotor
A technology for controlling torque gyroscopes and control systems, applied in the direction of auxiliary non-electric speed/acceleration control, etc., can solve problems such as inability to achieve results
- Summary
- Abstract
- Description
- Claims
- Application Information
AI Technical Summary
Problems solved by technology
Method used
Image
Examples
Embodiment Construction
[0066] For example, in the vibration test of the control moment gyro (CMG), it is found that the fundamental frequency of the rotor dynamic unbalance disturbance torque frequency actually acting on the low-speed frame is the high-speed rotor speed frequency, and its corresponding multiplier frequency components, including 3 , 5, 7 octaves. Since the CMG rotor speed is a constant value, the frequency of the rotor dynamic unbalance disturbance torque is a constant value, which is a set of periodic motion disturbance torque. In order to suppress this series of disturbance moments, thereby suppressing the CMG frame speed fluctuation, in the traditional double-loop PI control system, a feed-forward compensation module and an algorithm switching module are added, such as figure 1 shown.
[0067] The main idea of feed-forward compensation is that for a dynamic system that moves periodically on a finite interval, the error amount of the previous cycle iteration is used to correct t...
PUM
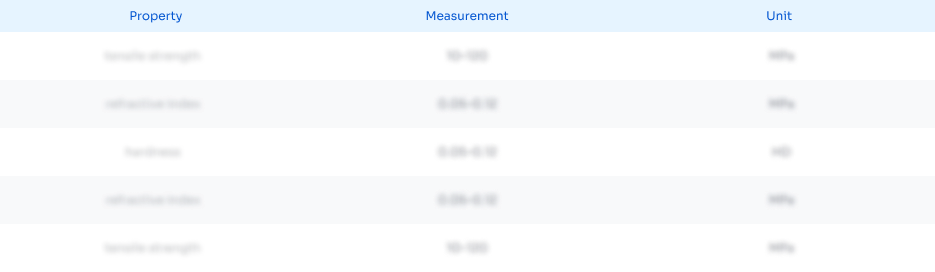
Abstract
Description
Claims
Application Information

- Generate Ideas
- Intellectual Property
- Life Sciences
- Materials
- Tech Scout
- Unparalleled Data Quality
- Higher Quality Content
- 60% Fewer Hallucinations
Browse by: Latest US Patents, China's latest patents, Technical Efficacy Thesaurus, Application Domain, Technology Topic, Popular Technical Reports.
© 2025 PatSnap. All rights reserved.Legal|Privacy policy|Modern Slavery Act Transparency Statement|Sitemap|About US| Contact US: help@patsnap.com