Wind driven generator gearbox optimal design method based on multi-body multi-force dynamics
A wind turbine, optimized design technology, applied in the direction of calculation, electrical digital data processing, special data processing applications, etc., can solve the problems of uncertain dynamic performance, local resonance, and hidden dangers of gearbox long-term operation, so as to ensure dynamic performance , to avoid the effect of resonance
- Summary
- Abstract
- Description
- Claims
- Application Information
AI Technical Summary
Problems solved by technology
Method used
Image
Examples
Embodiment Construction
[0021] The present invention will be further described below in conjunction with the accompanying drawings and specific embodiments.
[0022] Such as Figure 1 to Figure 3 As shown, the wind turbine gearbox optimization design method based on multi-body and multi-mechanics in this embodiment includes the following steps:
[0023] S01. Establish a dynamic model of the wind turbine drive chain, wherein each component in the gearbox is modeled with a flexible body;
[0024] S02. Carry out dynamic analysis on the established dynamic model of the wind turbine drive chain, and screen and check the resonance frequency of each component in the wind turbine gearbox. If there is a resonance frequency, proceed to the next step;
[0025] S03. Optimizing the design of the gearbox components corresponding to the resonance frequency: adjusting the low-order modal frequency by modifying the size or structure of the corresponding gearbox components;
[0026] S04. Steps S01 to S03 are cyclica...
PUM
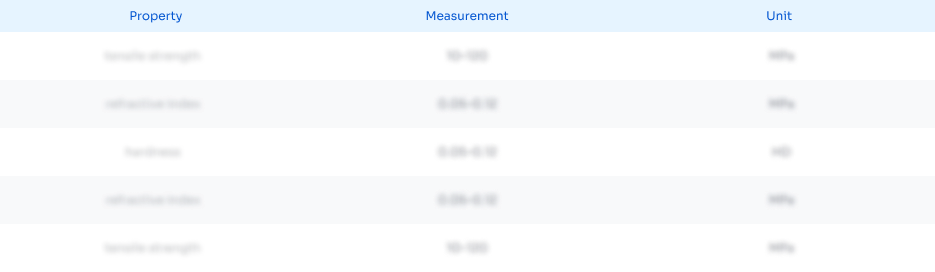
Abstract
Description
Claims
Application Information

- Generate Ideas
- Intellectual Property
- Life Sciences
- Materials
- Tech Scout
- Unparalleled Data Quality
- Higher Quality Content
- 60% Fewer Hallucinations
Browse by: Latest US Patents, China's latest patents, Technical Efficacy Thesaurus, Application Domain, Technology Topic, Popular Technical Reports.
© 2025 PatSnap. All rights reserved.Legal|Privacy policy|Modern Slavery Act Transparency Statement|Sitemap|About US| Contact US: help@patsnap.com