Composite coagulant used for treating printing and dyeing waste water and preparing method thereof
A printing and dyeing wastewater and coagulant technology, applied in the field of water treatment, can solve the problems of poor dye decolorization effect, complicated preparation process, secondary pollution, etc., and achieve good decolorization performance, simple preparation process, and fast sedimentation speed
- Summary
- Abstract
- Description
- Claims
- Application Information
AI Technical Summary
Problems solved by technology
Method used
Image
Examples
Embodiment 1
[0017] to 100m 3 Add 50t of industrial by-product waste hydrochloric acid (HCl%=18.9%) successively in the heat preservation reactor, and 30t of aluminum-containing waste slag in the aluminum profile industry (Al 2 o 3 %=14.0%), 40 ℃ normal pressure insulation and stirring for 1h until the aluminum slag is completely dissolved to obtain Al 2 o 3 % = 5.2%, HCl% = 2.2% aluminum slag water; add 0.08tMTR2400 heavy metal scavenger, stir and react for 0.5h, plate and frame filter to obtain light yellow clear aluminum-containing liquid; add industrial grade CaCl 2 1t (CaO%=47%), fully stirred until completely dissolved, continued the normal pressure heat preservation and stirring reaction for 0.5h, and then discharged, the supernatant liquid after natural precipitation was the liquid composite coagulant, and the finished product Al was tested. 2 o 3 %=5.1%, CaO%=0.5%, HCl%=2.0%, insoluble %<0.4%.
Embodiment 2
[0019] to 100m 3 Add 40t (HCl%=26.4%) of industrial by-product waste hydrochloric acid successively in the thermal insulation reaction kettle, 20t (Al 2 o 3 %=19.3%), 50 ℃ normal pressure insulation and stirring for 1.5h until the aluminum slag is completely dissolved to obtain Al 2 o 3 % = 6.4%, HCl% = 3.0% aluminum slag water; add 0.06tMTR2400 heavy metal scavenger, stir and react for 0.5h, plate and frame filter to obtain light yellow clear aluminum-containing liquid; add industrial grade CaCl 2 1t (CaO%=47%), fully stirred until completely dissolved, continued the normal pressure heat preservation and stirring reaction for 0.75h, and then discharged, the supernatant liquid after natural precipitation was the liquid composite coagulant, and the finished product Al 2 o 3 %=6.3%, CaO%=0.7%, HCl%=2.8%, insoluble matter%<0.4%.
Embodiment 3
[0021] to 100m 3 Add 30t of industrial by-product waste hydrochloric acid (HCl%=33.7%) successively in the heat preservation reactor, and 10t of aluminum-containing waste residue in the aluminum profile industry (Al 2 o 3 %=28.6%), 60 ℃ normal pressure insulation and stirring for 2h until the aluminum slag is completely dissolved to obtain Al 2 o 3 % = 7.1%, HCl% = 4.6% aluminum slag water; add 0.04tMTR2400 heavy metal scavenger, stir and react for 0.5h, plate and frame filter to obtain light yellow clear aluminum-containing liquid; add industrial grade CaCl 2 0.6t (CaO% = 47%), fully stirred until completely dissolved, continued the normal pressure heat preservation and stirring reaction for 1 hour, and then discharged, the supernatant liquid after natural precipitation was the liquid composite coagulant, and the finished product Al 2 o 3 %=7.0%, CaO%=0.6%, HCl%=4.4%, insoluble matter%<0.4%.
[0022] Composite coagulant effect evaluation that the present invention makes ...
PUM
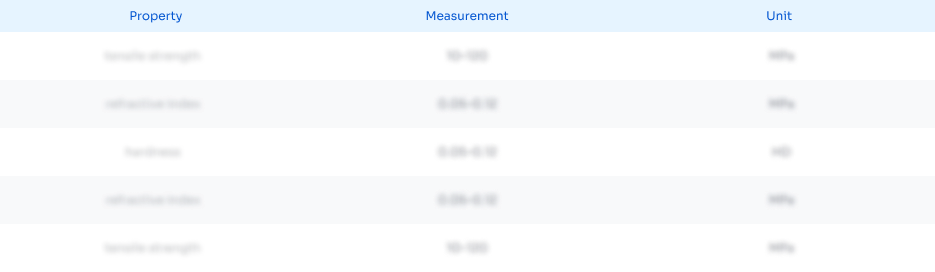
Abstract
Description
Claims
Application Information

- R&D
- Intellectual Property
- Life Sciences
- Materials
- Tech Scout
- Unparalleled Data Quality
- Higher Quality Content
- 60% Fewer Hallucinations
Browse by: Latest US Patents, China's latest patents, Technical Efficacy Thesaurus, Application Domain, Technology Topic, Popular Technical Reports.
© 2025 PatSnap. All rights reserved.Legal|Privacy policy|Modern Slavery Act Transparency Statement|Sitemap|About US| Contact US: help@patsnap.com