Production technology of air spinning cotton core filament covering yarn
A production process, air spinning technology, applied in yarn, textile and papermaking, etc., can solve the problems of poor wear resistance, poor shape retention, cloth wrinkle, etc., and achieve the effect of simple appearance, soft hand feeling and strong hygroscopicity
- Summary
- Abstract
- Description
- Claims
- Application Information
AI Technical Summary
Problems solved by technology
Method used
Examples
Embodiment 1
[0023] The production technology of embodiment 1 air-spun cotton core silk core-spun yarn, comprises the following processing steps:
[0024] S1: The core fiber is obtained by cleaning, carding, drawing and air spinning;
[0025] S2: Leather yarn is made from outsourcing fibers by cleaning, carding, drawing and roving;
[0026] S3: feeding the core yarn obtained in S1 and the leather yarn obtained in S2 to the core yarn device in the ring spinning equipment to make a core yarn;
[0027] S4: The core-spun yarn is produced through the winding process to obtain the finished air-spun cotton-core staple fiber core-spun yarn.
[0028] The core yarn is fed by the front roller of the spinning equipment and guided into the core yarn device through the active unwinding device, and the leather yarn is fed into the core yarn device after being drafted in the spinning process.
[0029] The fineness of the core yarn obtained by air spinning is 25 English.
[0030] The rotating speed of t...
Embodiment 2
[0036] The difference between embodiment 2 and embodiment 1 is that the fineness of the core yarn obtained by air spinning in embodiment 2 is Ne 23.
[0037] In S1, the rotating speed of the rotor in the process of producing core yarn by air spinning is 8100r / min.
[0038] The process parameters of the spinning process of the core-spun yarn are as follows: the total draft ratio is 40, the draft ratio in the rear area is 1.4, the spindle speed is 14200r / min, the twist is 440TPM, the roller center distance is 55mm and 56mm, and the spacer is 8mm.
[0039] The total draft ratio of leather yarn roving process is 6.4, the rear zone draft ratio is 1.244, the twist coefficient is 110, the dry basis weight is 8g / 10m, and the spindle speed is 760r / min.
[0040] The weight of the core yarn accounts for 50% of the total yarn of the air-spun core yarn cotton staple core yarn.
Embodiment 3
[0042] The difference between embodiment 3 and embodiment 2 is: the fineness of the core yarn obtained by air spinning is 21 Nem.
[0043] In S1, the rotating speed of the rotor in the core yarn production process by air spinning is 8000r / min.
[0044] The process parameters of the spinning process of the core-spun yarn are as follows: the total draft ratio is 37, the draft ratio in the rear area is 1.2, the spindle speed is 14000r / min, the twist is 430TPM, the center distance of the rollers is 51mm and 53mm respectively, and the spacer is 7.5mm.
[0045] The total draft ratio of leather yarn roving process is 6.3, the rear zone draft ratio is 1.242, the twist coefficient is 108, the dry basis weight is 7.5g / 10m, and the spindle speed is 750r / min.
[0046] The weight of the core yarn accounts for 60% of the total yarn of the air-spun core yarn cotton staple core yarn.
PUM
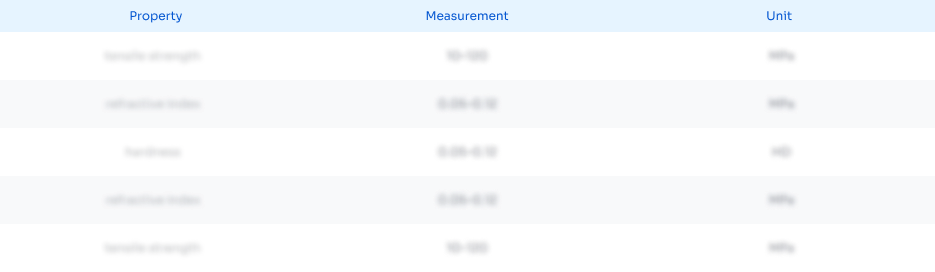
Abstract
Description
Claims
Application Information

- R&D
- Intellectual Property
- Life Sciences
- Materials
- Tech Scout
- Unparalleled Data Quality
- Higher Quality Content
- 60% Fewer Hallucinations
Browse by: Latest US Patents, China's latest patents, Technical Efficacy Thesaurus, Application Domain, Technology Topic, Popular Technical Reports.
© 2025 PatSnap. All rights reserved.Legal|Privacy policy|Modern Slavery Act Transparency Statement|Sitemap|About US| Contact US: help@patsnap.com