The production process of materials suitable for diesel engine cylinder blocks and cylinder heads
A diesel engine and production process technology, applied in engine components, machines/engines, cylinder heads, etc., can solve the problems of proportional control, high production cost of cylinder block and cylinder head castings, and low strength of gray cast iron, and improve tensile strength. Strength and hardness, improve casting process performance, good casting processability
- Summary
- Abstract
- Description
- Claims
- Application Information
AI Technical Summary
Problems solved by technology
Method used
Examples
Embodiment 1
[0053] A kind of production technology of diesel engine block, cylinder cover material, comprises the steps:
[0054] Step (1), equipment preparation: the equipment adopts medium frequency induction furnace;
[0055] Step (2), ingredients: in parts by weight, 37 parts of steel scrap, 20 parts of returned material, 38 parts of iron filings cake, and 1.5 parts of ZT-2 cast iron recarburizer;
[0056] Step (3), feeding: first add 28% of the cast iron recarburizer to the bottom of the electric furnace, and then add iron scraps, scrap steel and returned materials in sequence, and the remaining recarburizer should be added together with the returned materials. Before the remaining 9% of the charge is added, it is required that there is always a return charge to hold down the recarburizer;
[0057] Step (4), melting: power on and melt immediately after adding the returned material, use full power and uninterrupted melting during melting, control the melting temperature of the electr...
Embodiment 2
[0062] A kind of production technology of diesel engine block, cylinder cover material, comprises the steps:
[0063] Step (1), equipment preparation: the equipment adopts medium frequency induction furnace;
[0064] Step (2), ingredients: in parts by weight, 40 parts of steel scrap, 24 parts of returned material, 41 parts of iron filings cake, and 1.8 parts of ZT-2 cast iron recarburizer;
[0065] Step (3), feeding: first add 32% of the cast iron recarburizer to the bottom of the electric furnace, then add iron scraps, steel scrap and returned materials in sequence, and the remaining recarburizer should be added together with the returned materials. The remaining 11% of the furnace charge should be added before the remaining 11%, and it is required that there is always a return charge to hold down the carburizer;
[0066] Step (4), melting: power on and melt immediately after adding the returned materials, use full power and uninterrupted melting when melting, control the me...
Embodiment 3
[0071] A kind of production technology of diesel engine block, cylinder cover material, comprises the steps:
[0072] Step (1), equipment preparation: the equipment adopts medium frequency induction furnace;
[0073] Step (2), ingredients: in parts by weight, 38 parts of steel scrap, 21 parts of returned materials, 40 parts of iron filings, and 1.6 parts of ZT-2 cast iron recarburizer;
[0074] Step (3), feeding: first add 31% of the cast iron recarburizer to the bottom of the electric furnace, and then add iron scraps, scrap steel and returned materials in sequence, and the remaining recarburizer should be added together with the returned materials. The remaining 9.5% of the furnace charge should be added before, and it is required that there is always a return charge to hold down the carburizer;
[0075] Step (4), melting: power on and melt immediately after adding the returned material, use full power and uninterrupted melting during melting, control the melting temperatur...
PUM
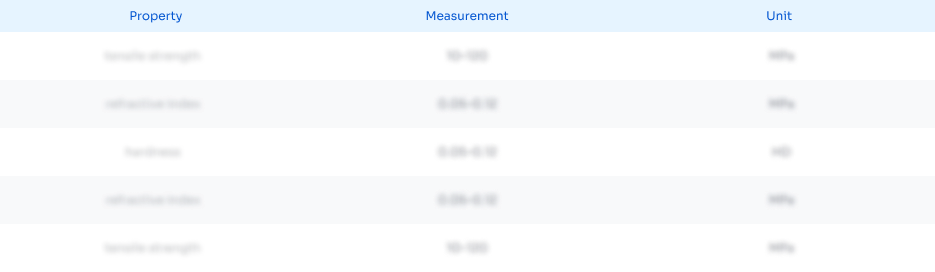
Abstract
Description
Claims
Application Information

- Generate Ideas
- Intellectual Property
- Life Sciences
- Materials
- Tech Scout
- Unparalleled Data Quality
- Higher Quality Content
- 60% Fewer Hallucinations
Browse by: Latest US Patents, China's latest patents, Technical Efficacy Thesaurus, Application Domain, Technology Topic, Popular Technical Reports.
© 2025 PatSnap. All rights reserved.Legal|Privacy policy|Modern Slavery Act Transparency Statement|Sitemap|About US| Contact US: help@patsnap.com