Preparation method of hydroisomerization/cracking catalyst and catalyst
A cracking catalyst and hydrogen isomerization technology, applied in the direction of physical/chemical process catalysts, molecular sieve catalysts, chemical instruments and methods, etc., can solve the problems of lower product performance, lower yield of target products, and reduced yield, etc., to achieve Effects of increasing diesel content and lubricating base oil content, excellent isomerization performance, and good cracking performance
- Summary
- Abstract
- Description
- Claims
- Application Information
AI Technical Summary
Problems solved by technology
Method used
Image
Examples
Embodiment 1
[0029] Take 100 g of sodium ZSM-23 molecular sieve containing isopropylamine template, place it in 3 L of NaOH solution with a concentration of 0.2 mol / L, treat it at 80 ° C for 180 min, filter, wash until the eluate is neutral, dry and Roasting removes the template agent; the resulting product is placed in 2L of NH with a concentration of 0.5mol / L 4 NO 3 In the solution, exchange at 60°C for 180min, filter, wash with deionized water until the eluent is neutral, exchange continuously (repeat the above operation) twice, dry at 120°C, and roast at 550°C for 24h to obtain Hydrogen ZSM-23 molecular sieve (H-ZSM-23). Take 30g of alumina (γ-Al 2 o 3 ) and mix it evenly, add 80g5wt.%HNO 3 Solution, kneaded at room temperature for 2 hours, extruded at room temperature with an automatic extruder, dried naturally, then dried at 120°C for 4 hours, and calcined at 550°C for 8 hours to obtain a molecular sieve carrier (H-ZSM-23 carrier). With 10mL of chloroplatinic acid (H 2 PtCl 6 ...
Embodiment 2
[0031] Take 100g of sodium ZSM-23 molecular sieve containing isopropylamine template, put it in 3L NaOH solution with a concentration of 0.4mol / L, treat it at 80°C for 180min, filter, wash until the eluent is neutral, dry and Roasting removes the template agent; the resulting product is placed in 2L of NH with a concentration of 0.5mol / L 4 NO 3In the solution, exchange at 60°C for 180min, filter, wash with deionized water until the eluent is neutral, exchange continuously (repeat the above operation) twice, dry at 120°C, and roast at 550°C for 24h to obtain Hydrogen ZSM-23 molecular sieve (H-ZSM-23). Take 30g of alumina (γ-Al 2 o 3 ) and mix it evenly, add 80g5wt.%HNO 3 Solution, kneaded at room temperature for 2 hours, extruded at room temperature with an automatic extruder, dried naturally, then dried at 120°C for 4 hours, and calcined at 550°C for 8 hours to obtain a molecular sieve carrier (H-ZSM-23 carrier). With 10mL of chloroplatinic acid (H 2 PtCl 6 ) solution t...
Embodiment 3
[0033] Take 100 g of sodium ZSM-23 molecular sieve containing isopropylamine template, place it in 3 L of NaOH solution with a concentration of 0.6 mol / L, treat it at 80 ° C for 180 min, filter, wash until the eluate is neutral, dry and Roasting removes the template agent; the resulting product is placed in 2L of NH with a concentration of 0.5mol / L 4 NO 3 In the solution, exchange at 60°C for 180min, filter, wash with deionized water until the eluent is neutral, exchange continuously (repeat the above operation) twice, dry at 120°C, and roast at 550°C for 24h to obtain Hydrogen ZSM-23 molecular sieve (H-ZSM-23). Take 30g of alumina (γ-Al 2 o 3 ) and mix it evenly, add 80g5wt.%HNO 3 Solution, kneaded at room temperature for 2 hours, extruded at room temperature with an automatic extruder, dried naturally, then dried at 120°C for 4 hours, and calcined at 550°C for 8 hours to obtain a molecular sieve carrier (H-ZSM-23 carrier). With 10mL of chloroplatinic acid (H 2 PtCl 6 ...
PUM
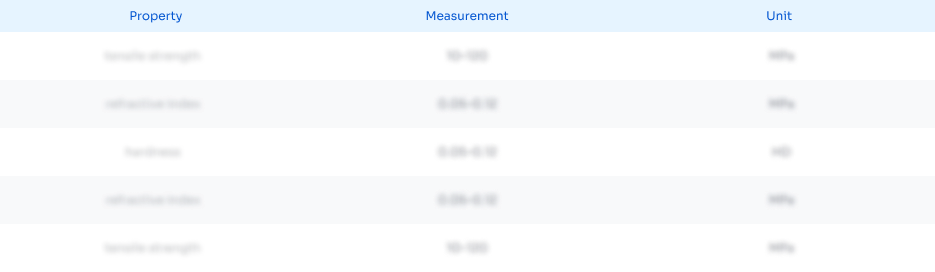
Abstract
Description
Claims
Application Information

- R&D
- Intellectual Property
- Life Sciences
- Materials
- Tech Scout
- Unparalleled Data Quality
- Higher Quality Content
- 60% Fewer Hallucinations
Browse by: Latest US Patents, China's latest patents, Technical Efficacy Thesaurus, Application Domain, Technology Topic, Popular Technical Reports.
© 2025 PatSnap. All rights reserved.Legal|Privacy policy|Modern Slavery Act Transparency Statement|Sitemap|About US| Contact US: help@patsnap.com