A combined optimization system for high temperature flue gas and heat
A high-temperature flue gas and joint optimization technology, applied in the field of industrial waste heat utilization, can solve the problems of joint energy consumption without considering heat, high production costs, and low utilization rate of high-temperature flue gas waste heat, so as to increase coal consumption and improve utilization rate, the effect of reducing consumption
- Summary
- Abstract
- Description
- Claims
- Application Information
AI Technical Summary
Problems solved by technology
Method used
Image
Examples
Embodiment Construction
[0019] The technical solutions of the present invention will be further described below in conjunction with the accompanying drawings and through specific embodiments.
[0020] On the basis of the existing technology, the first production device A and the second production device B are used in combination, and the present invention mainly improves the partial coils of the superheating section and the evaporation section of the high-temperature flue gas waste heat boiler of the second production device B , provides a high-temperature flue gas thermal optimization system, the structure of the high-temperature flue gas thermal optimization system is as follows image 3 As shown, it includes a first production device A and a second production device B, the first production device A includes a process material pump 1, a heat exchanger group 2 and a heating furnace 3 connected by pipelines, and the second production device B includes a waste heat boiler 4 with a superheating section...
PUM
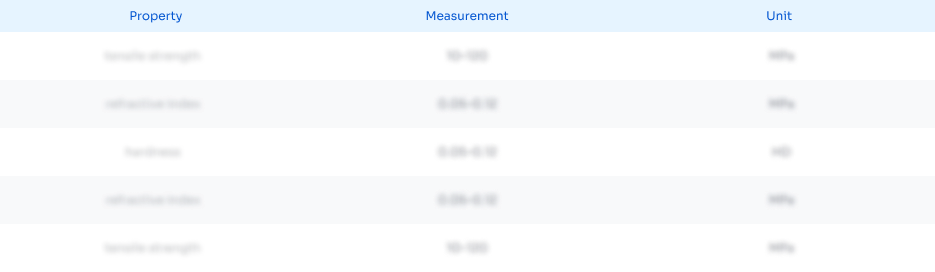
Abstract
Description
Claims
Application Information

- R&D Engineer
- R&D Manager
- IP Professional
- Industry Leading Data Capabilities
- Powerful AI technology
- Patent DNA Extraction
Browse by: Latest US Patents, China's latest patents, Technical Efficacy Thesaurus, Application Domain, Technology Topic, Popular Technical Reports.
© 2024 PatSnap. All rights reserved.Legal|Privacy policy|Modern Slavery Act Transparency Statement|Sitemap|About US| Contact US: help@patsnap.com