Sealing structure of turbo-charged direct injection engine exhaust system
A technology of exhaust system and sealing structure, applied in the direction of engine sealing, engine sealing device, engine components, etc., can solve the problems of exhaust manifold flange deformation and cracking, gasket sealing failure, bolt fracture, etc., to avoid Fracture failure, meet the sealing requirements, and avoid the effect of bolt fracture
- Summary
- Abstract
- Description
- Claims
- Application Information
AI Technical Summary
Problems solved by technology
Method used
Image
Examples
Embodiment Construction
[0019] The present invention will be described in detail below in conjunction with the accompanying drawings.
[0020] like Figure 2 to Figure 6 The sealing structure of the exhaust system of the supercharged direct injection engine shown includes a cylinder head flange 1 , four gaskets 2 and an exhaust manifold flange 3 .
[0021] like figure 2 , image 3 As shown, the edge of the cylinder head flange 1 is provided with a plurality of cylinder head bolt connection holes 14, and the cylinder head flange 1 is provided with four exhaust ports 11 (corresponding to a four-cylinder supercharged direct injection engine). Sealing grooves 12 (a total of four sealing grooves) are machined on the edges of the flange 1 corresponding to each exhaust port 11, the depth of the sealing grooves is a=5mm, and the edges of the sealing grooves 12 are provided with three limiting grooves 13. The connecting lines of the three limiting slots 13 are perpendicular to each other.
[0022] like ...
PUM
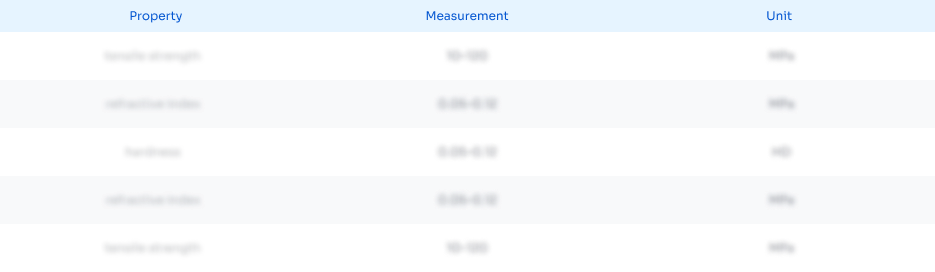
Abstract
Description
Claims
Application Information

- R&D Engineer
- R&D Manager
- IP Professional
- Industry Leading Data Capabilities
- Powerful AI technology
- Patent DNA Extraction
Browse by: Latest US Patents, China's latest patents, Technical Efficacy Thesaurus, Application Domain, Technology Topic, Popular Technical Reports.
© 2024 PatSnap. All rights reserved.Legal|Privacy policy|Modern Slavery Act Transparency Statement|Sitemap|About US| Contact US: help@patsnap.com