Method for machining off-axis aspherical mirror
An off-axis aspheric surface and processing method technology, which is applied to the processing field of off-axis aspheric mirrors, can solve problems such as low efficiency of workpiece edge processing, and achieve the effects of increasing processing difficulty and overcoming slow error convergence.
- Summary
- Abstract
- Description
- Claims
- Application Information
AI Technical Summary
Problems solved by technology
Method used
Image
Examples
Embodiment
[0036] Example: see attached Image 6 As shown, the shape of the off-axis aspheric surface as shown in the off-axis aspheric mirror body 18 in the figure, its structural parameters: radius of curvature R=407.6mm, conic constant K=-0.48, diameter of the arc side wall of the off-axis mirror is 120mm, The distance between the parallel side walls of the off-axis mirror is 86mm, and the off-axis distance is 30mm. According to the structure of the off-axis mirror body, the diameter of the rotating parent body is 230mm, and the through hole 14 for inlaying the daughter body structure is excavated on the blank of the rotating aspheric surface parent body 13; the blank of the off-axis aspheric mirror body 18 is placed in the through hole In the hole 14, an off-axis aspheric mirror body and a rotating aspherical parent body are combined into a cylindrical integral workpiece by using an optical adhesive; the initial spherical surface 5 for processing the rotating aspheric surface is proc...
PUM
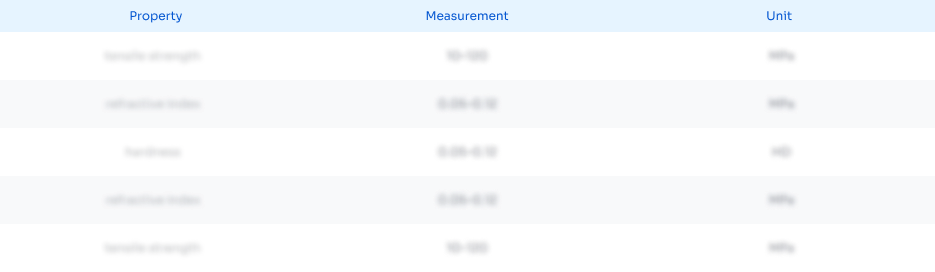
Abstract
Description
Claims
Application Information

- Generate Ideas
- Intellectual Property
- Life Sciences
- Materials
- Tech Scout
- Unparalleled Data Quality
- Higher Quality Content
- 60% Fewer Hallucinations
Browse by: Latest US Patents, China's latest patents, Technical Efficacy Thesaurus, Application Domain, Technology Topic, Popular Technical Reports.
© 2025 PatSnap. All rights reserved.Legal|Privacy policy|Modern Slavery Act Transparency Statement|Sitemap|About US| Contact US: help@patsnap.com