Automatic-tracking-based profile measurement system and method for free-form-surface optical element
An optical element and automatic tracking technology, which is applied in the field of measurement of aspheric surfaces and free surfaces, can solve problems such as surface damage and achieve the effect of compensating for damage
- Summary
- Abstract
- Description
- Claims
- Application Information
AI Technical Summary
Problems solved by technology
Method used
Image
Examples
Embodiment
[0043] In the embodiment, a concave mirror with known design parameters is used to verify the accuracy of the measurement method. First place the concave mirror on the turntable, and then drive the turntable to move 18mm along the X-axis direction at a speed of 1mm / s through the pneumatic platform, then move 0.1mm along the Y-axis direction at a speed of 1mm / s, and then continue to move in the opposite direction along the X-axis Moving at the same speed, it moves back and forth in this way to realize S-shaped scanning, and the scanning range is 18mm*18mm. The result is as Figure 4 As shown, the difference between the measured parameters and the design parameters is about ±2um, which is within the tolerance range given by the concave mirror manufacturer.
PUM
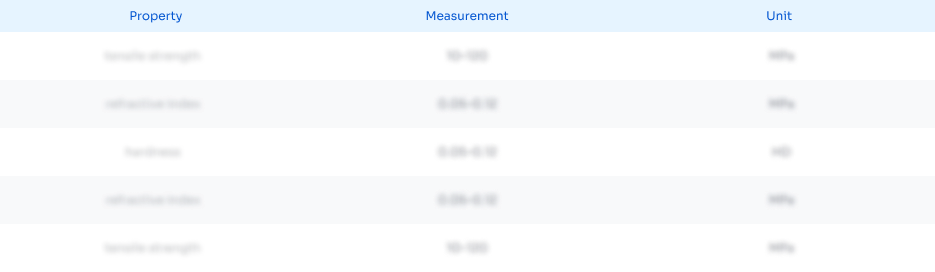
Abstract
Description
Claims
Application Information

- R&D
- Intellectual Property
- Life Sciences
- Materials
- Tech Scout
- Unparalleled Data Quality
- Higher Quality Content
- 60% Fewer Hallucinations
Browse by: Latest US Patents, China's latest patents, Technical Efficacy Thesaurus, Application Domain, Technology Topic, Popular Technical Reports.
© 2025 PatSnap. All rights reserved.Legal|Privacy policy|Modern Slavery Act Transparency Statement|Sitemap|About US| Contact US: help@patsnap.com