Preparation method of high-coating-ratio zirconium silicate coated ceramic pigment and product prepared therethrough
A ceramic pigment, zirconium silicate technology, applied in chemical instruments and methods, fibrous fillers, inorganic pigment treatment, etc., can solve the problems of blocking color development, loss of color development contribution, limiting the application of zirconium silicate, etc. The effect of wrapping rate and improving hair color strength
- Summary
- Abstract
- Description
- Claims
- Application Information
AI Technical Summary
Problems solved by technology
Method used
Examples
Embodiment 1
[0028] In this embodiment, a method for preparing a high-encapsulation rate zirconium silicate-encapsulated ceramic pigment, the steps are as follows:
[0029] (1) Preparation of suspension
[0030] Adding 6g of carbon black to 300g of ZrCl with a concentration of 30wt% 4 In the ethanol solution, add 2g of 10wt% CTAB ethanol solution to promote the dispersion of carbon black, and stir to obtain a suspension;
[0031] (2) Preparation of zirconium coating
[0032] Put the suspension in an oven at 60°C to volatilize ethanol until it is completely dry to obtain a primary powder; then put the primary powder and excess concentrated ammonia water into two containers respectively, and then put the two containers into an upside-down button at the same time In an airtight plastic container, leave it to stand for reaction for 12 hours to obtain a jelly-like substance coated with a zirconium hydroxide coating on the surface of carbon black;
[0033] (3) Preparation of silicic acid coat...
Embodiment 2
[0039] In this example, a method for preparing a high-encapsulation rate zirconium silicate-encapsulated ceramic pigment differs from Example 1 in that in step (2), the suspension is placed in a vacuum drying oven, and ethanol is volatilized at a temperature of 30°C , to obtain a powder after complete drying, and then feed 10vol% NH 3 -N 2 , Let stand for 12h.
[0040] The zirconium silicate wrapped carbon black material obtained in this example has a wrapping rate of 93%, and the chromaticity is: L*=24.85, a*=-0.54, b*=-1.43.
Embodiment 3
[0042] In this embodiment, a method for preparing a high-encapsulation rate zirconium silicate-encapsulated ceramic pigment, the steps are as follows:
[0043] (1) Preparation of suspension
[0044] Adding 10 grams of cadmium sulfur selenide to 50 g of ZrCl with a concentration of 30 wt % 4 In the ethanol solution, add 1g10wt% CTAB ethanol solution to promote the dispersion of cadmium sulfoselenide, and obtain a suspension after ultrasonication and stirring;
[0045] (2) Preparation of zirconium coating
[0046]Put the suspension in a 60°C oven to volatilize the ethanol until it is completely dry to obtain a primary powder; then put the primary powder and concentrated ammonia water into two containers respectively, and then put the two containers into an upside-down container at the same time , in an airtight plastic container, leave it to stand for 12 hours to react, and obtain a jelly-like substance coated with a zirconium hydroxide coating layer on the surface of cadmium ...
PUM
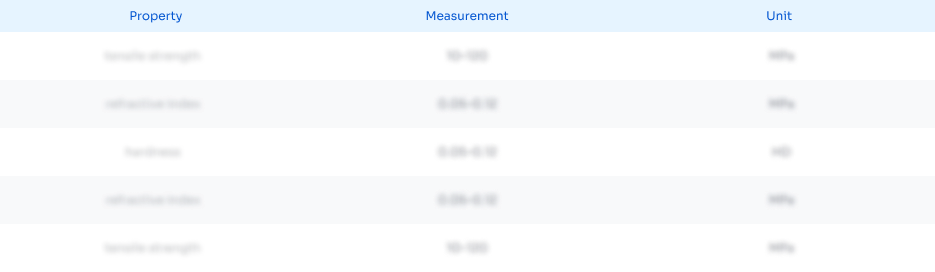
Abstract
Description
Claims
Application Information

- R&D
- Intellectual Property
- Life Sciences
- Materials
- Tech Scout
- Unparalleled Data Quality
- Higher Quality Content
- 60% Fewer Hallucinations
Browse by: Latest US Patents, China's latest patents, Technical Efficacy Thesaurus, Application Domain, Technology Topic, Popular Technical Reports.
© 2025 PatSnap. All rights reserved.Legal|Privacy policy|Modern Slavery Act Transparency Statement|Sitemap|About US| Contact US: help@patsnap.com