High thermal conductive and insulating material and preparation method thereof
An insulating material and high thermal conductivity technology, applied in the field of high thermal conductivity insulating material and its preparation, can solve the problems of cumbersome synthesis method, inability of insulating thermal conductivity material to meet industrialization needs, and high requirements on two-phase compatibility, and achieves reasonable composition and curing. Good effect, good insulation effect
- Summary
- Abstract
- Description
- Claims
- Application Information
AI Technical Summary
Problems solved by technology
Method used
Examples
Embodiment 1
[0017] (1) In parts by mass, add 100 parts of bis((3,4-epoxycyclohexyl)methyl)adipate to 150 parts of ethylene glycol, stir at 110°C for 5 minutes, then add 6 parts of 3 -Tridecafluorohexylpropene, 10 parts of N-(3-hydroxyphenyl)acetamide, adjust the temperature to 120°C, stir for 35 minutes, then add 0.6 parts of glutaryl hydrazide and 1.1 parts of 4-tert-butylphenylacetylene, Stir for 2 hours; Add 6 parts of alumina again; Stir for 85 minutes to obtain epoxy material;
[0018] (2) In terms of parts by mass, mix 15 parts of graphene and 1 part of polyvinylpyrrolidone to obtain pretreated graphene; add 18 parts of N-acetyl p-aminophenol to 20 parts of ethanol, stir and mix for 40 minutes, and then Add 4 parts of silicon nitride, mix for 1 hour, then add the above-mentioned pretreated graphene, and stir at 50°C for 25 minutes to obtain a filler mixture;
[0019] (3) In parts by mass, add 1 part of the filler mixture prepared in step (2) to 5 parts of epoxy material prepared in...
Embodiment 2
[0022] (1) In parts by mass, add 100 parts of bis((3,4-epoxycyclohexyl)methyl)adipate to 150 parts of ethylene glycol, stir at 110°C for 5 minutes, then add 6 parts of 3 -Tridecafluorohexylpropene, 10 parts of N-(3-hydroxyphenyl)acetamide, adjust the temperature to 120°C, stir for 35 minutes, then add 0.6 parts of glutaryl hydrazide and 1.1 parts of 4-tert-butylphenylacetylene, Stir for 2 hours; Add 6 parts of alumina again; Stir for 85 minutes to obtain epoxy material;
[0023] (2) In terms of parts by mass, mix 15 parts of graphene and 1 part of polyvinylpyrrolidone to obtain pretreated graphene; add 18 parts of N-acetyl p-aminophenol to 20 parts of ethanol, stir and mix for 40 minutes, and then Add 4 parts of silicon nitride, mix for 1 hour, then add the above-mentioned pretreated graphene, and stir at 50°C for 25 minutes to obtain a filler mixture;
[0024] (3) In parts by mass, add 1 part of the filler mixture prepared in step (2) to 6 parts of epoxy material prepared in...
Embodiment 3
[0026] (1) In parts by mass, add 100 parts of bis((3,4-epoxycyclohexyl)methyl)adipate to 150 parts of ethylene glycol, stir at 110°C for 5 minutes, then add 6 parts of 3 -Tridecafluorohexylpropene, 10 parts of N-(3-hydroxyphenyl)acetamide, adjust the temperature to 120°C, stir for 35 minutes, then add 0.6 parts of glutaryl hydrazide and 1.1 parts of 4-tert-butylphenylacetylene, Stir for 2 hours; Add 6 parts of alumina again; Stir for 85 minutes to obtain epoxy material;
[0027] (2) In terms of parts by mass, mix 15 parts of graphene and 1 part of polyvinylpyrrolidone to obtain pretreated graphene; add 18 parts of N-acetyl p-aminophenol to 20 parts of ethanol, stir and mix for 40 minutes, and then Add 4 parts of silicon nitride, mix for 1 hour, then add the above-mentioned pretreated graphene, and stir at 50°C for 25 minutes to obtain a filler mixture;
[0028] (3) In parts by mass, add 1 part of the filler mixture prepared in step (2) to 7 parts of epoxy material prepared in...
PUM
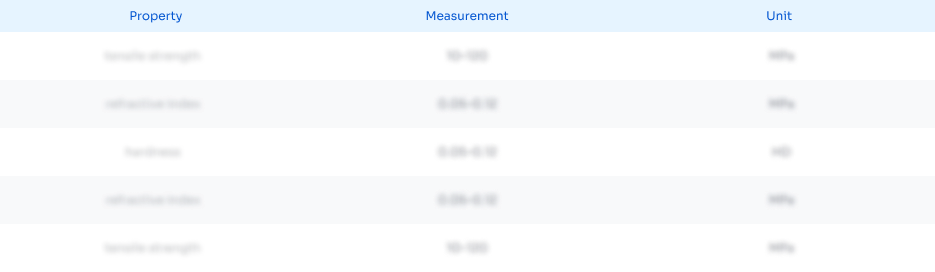
Abstract
Description
Claims
Application Information

- Generate Ideas
- Intellectual Property
- Life Sciences
- Materials
- Tech Scout
- Unparalleled Data Quality
- Higher Quality Content
- 60% Fewer Hallucinations
Browse by: Latest US Patents, China's latest patents, Technical Efficacy Thesaurus, Application Domain, Technology Topic, Popular Technical Reports.
© 2025 PatSnap. All rights reserved.Legal|Privacy policy|Modern Slavery Act Transparency Statement|Sitemap|About US| Contact US: help@patsnap.com