Polybutylene foam material and preparing method thereof
A foaming material, polybutene technology, applied in the field of modified plastics, can solve the problems of low foaming ratio, easy cell rupture, low melt strength, etc., and achieve good mechanical properties, uniform cell distribution, widening Effects in the field of application
- Summary
- Abstract
- Description
- Claims
- Application Information
AI Technical Summary
Problems solved by technology
Method used
Image
Examples
Embodiment 1
[0070] The present embodiment provides that the preparation method of polybutene foaming material is the extrusion foaming method, and proceeds according to the following steps:
[0071] Step 1, place the polybutene and talcum powder with 93% identical content used in the experiment in a vacuum drying oven at 50° C. for 24 hours;
[0072] Step 2, premixing the raw materials according to the formula ratio, so that the raw materials are preliminarily mixed evenly to obtain a premixed material, wherein:
[0073] Described formula ratio is by weight percentage, is made up of following raw materials: polybutene is 90.45%, foaming agent AC is 1.4%, foaming aid ZnO is 0.4%, talcum powder (325 orders) is 6%, anti- Oxygen agent 1010 is 0.1%, dicumyl peroxide DCP is 0.15%, Hst is 0.5%, glyceryl monostearate is 1%, and the total amount of raw materials is 100%.
[0074] Step 3, adding the premix obtained in step 2 into a single-screw extruder for mixing and extrusion foaming, wherein: ...
Embodiment 2
[0080] The present embodiment provides that the preparation method of polybutene foaming material is the extrusion foaming method, and proceeds according to the following steps:
[0081] Step 1, place the polybutene and talcum powder with 93% identical content used in the experiment in a vacuum drying oven at 50° C. for 24 hours;
[0082] Step 2, premixing the raw materials according to the formula ratio, so that the raw materials are preliminarily mixed evenly to obtain a premixed material, wherein:
[0083] Described formula ratio is by weight percent, is made up of following raw material: polybutene is 87.25%, foaming agent AC is 5%, foaming aid ZnO is 1%, talcum powder (325 order) is 6%, anti- Oxygen agent 1010 is 0.1%, dicumyl peroxide DCP is 0.15%, Hst is 0.5%, glyceryl monostearate is 1%, and the total amount of raw materials is 100%.
[0084] Step 3, adding the premix obtained in step 2 into a single-screw extruder for mixing and extrusion foaming, wherein:
[0085] ...
Embodiment 3
[0090] The present embodiment provides that the preparation method of polybutene foaming material is the injection foaming method, and proceeds according to the following steps:
[0091] Step 1, place polybutene and talcum powder with an isotropic content of 88% used in the experiment in a vacuum drying oven at 50° C. for 24 hours;
[0092] Step 2, premixing the raw materials according to the formula ratio, so that the raw materials are preliminarily mixed evenly to obtain a premixed material, wherein:
[0093] Described formula ratio is by weight percentage, is made up of following raw materials: polybutene is 88.45%, foaming agent AC is 2.5%, foaming aid ZnO is 0.5%, talcum powder (325 order) 7%, antioxidant Agent 1010 is 0.1%, dicumyl peroxide DCP is 0.15%, Hst is 0.3%, glyceryl monostearate is 1%, and the total amount of raw materials is 100%.
[0094] Step 3: Add the premixed material obtained in Step 2 into the barrel, knead with the screw and inject it into the mold ca...
PUM
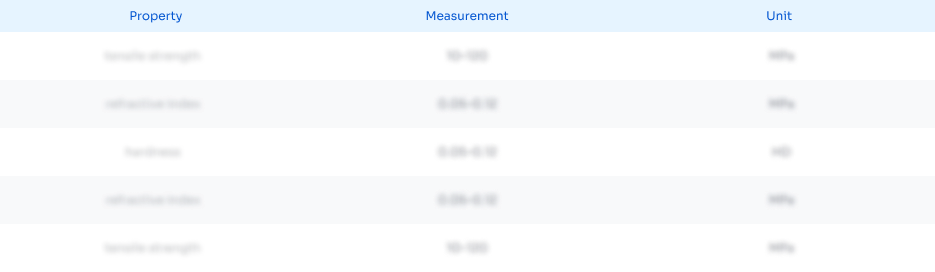
Abstract
Description
Claims
Application Information

- R&D Engineer
- R&D Manager
- IP Professional
- Industry Leading Data Capabilities
- Powerful AI technology
- Patent DNA Extraction
Browse by: Latest US Patents, China's latest patents, Technical Efficacy Thesaurus, Application Domain, Technology Topic, Popular Technical Reports.
© 2024 PatSnap. All rights reserved.Legal|Privacy policy|Modern Slavery Act Transparency Statement|Sitemap|About US| Contact US: help@patsnap.com