Sand mould casting technology using filter screens instead of washburn cores
A technology of sand casting and filter screen, which is applied in the removal of sand casting risers and in the field of sand casting technology. It can solve the problems of time-consuming removal of risers, high labor intensity, and low production efficiency, so as to increase market share and reduce labor intensity. , The effect of reducing the scrap rate
- Summary
- Abstract
- Description
- Claims
- Application Information
AI Technical Summary
Problems solved by technology
Method used
Examples
Embodiment 1
[0019] In an embodiment of the present invention, a sand casting process in which a filter screen is used instead of an easy-to-cut sheet comprises the following steps:
[0020] Step 1. Make the upper mold and the lower mold of the hammerhead sand mold, and reserve the position of the ingate.
[0021] Step 2: Install a filter screen between the riser and the hammer head pattern, and integrate the filter screen with the hammer head shape; install a filter screen on the sprue at a position close to the sprue cup. Wherein, the filter screen is obtained by weaving glass filaments into a square mesh with a hole diameter of 3 mm, coating with high-temperature resistant ceramic slurry, and sintering at high temperature. The filter screen fixed between the riser and the shape of the hammer has the effect of controlling the height of the stub of the riser, and the height of the stub of the riser can be controlled to 1-2 mm.
[0022] Step 3, paint the upper and lower molds of the hamme...
Embodiment 2
[0026] In an embodiment of the present invention, a sand casting process in which a filter screen is used instead of an easy-to-cut sheet comprises the following steps:
[0027] Step 1. Make the upper mold and the lower mold of the hammerhead sand mold, and reserve the position of the ingate.
[0028] Step 2: Install a filter screen between the riser and the hammer head pattern, and integrate the filter screen with the hammer head shape; install a filter screen on the sprue at a position close to the sprue cup. Wherein, the filter screen is obtained by weaving glass filaments into a square mesh with a pore diameter of 5 mm, coating with high-temperature resistant ceramic slurry, and sintering at high temperature. The filter screen fixed between the riser and the shape of the hammer has the effect of controlling the height of the stub of the riser, and the height of the stub of the riser is 2-3mm.
[0029] Step 3, paint the upper mold and the lower mold of the hammerhead sand ...
Embodiment 3
[0033] In an embodiment of the present invention, a sand casting process in which a filter screen is used instead of an easy-to-cut sheet comprises the following steps:
[0034] Step 1. Make the upper mold and the lower mold of the hammerhead sand mold, and reserve the position of the ingate.
[0035] Step 2: Install a filter screen between the riser and the hammer head pattern, and integrate the filter screen with the hammer head shape; install a filter screen on the sprue at a position close to the sprue cup. Wherein, the filter screen is obtained by weaving glass filaments into a square grid with a hole diameter of 8 mm, coating with high-temperature resistant ceramic slurry, and sintering at high temperature. The filter screen fixed between the riser and the shape of the hammer has the effect of controlling the height of the stub of the riser, and the height of the stub of the riser is 3-4mm.
[0036] Step 3, paint the upper mold and the lower mold of the hammerhead sand ...
PUM
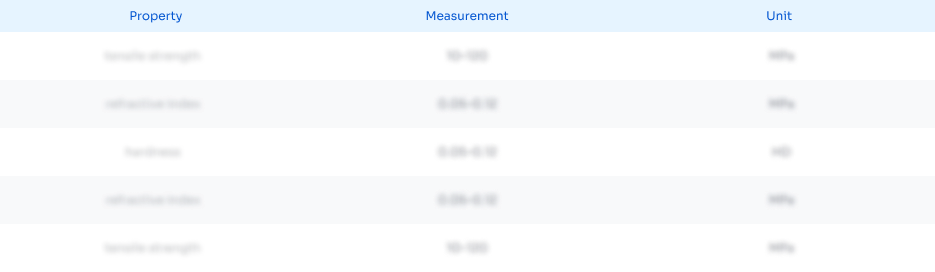
Abstract
Description
Claims
Application Information

- R&D
- Intellectual Property
- Life Sciences
- Materials
- Tech Scout
- Unparalleled Data Quality
- Higher Quality Content
- 60% Fewer Hallucinations
Browse by: Latest US Patents, China's latest patents, Technical Efficacy Thesaurus, Application Domain, Technology Topic, Popular Technical Reports.
© 2025 PatSnap. All rights reserved.Legal|Privacy policy|Modern Slavery Act Transparency Statement|Sitemap|About US| Contact US: help@patsnap.com