Preparation method of magnesium aluminate spinel for catalyst carrier
A magnesium-aluminum spinel and catalyst carrier technology, applied in chemical instruments and methods, physical/chemical process catalysts, metal/metal oxide/metal hydroxide catalysts, etc., can solve problems that are not safe and environmentally friendly, and are not suitable for large quantities Production and other problems, to achieve the effect of easy reaction, good application value and low temperature
- Summary
- Abstract
- Description
- Claims
- Application Information
AI Technical Summary
Problems solved by technology
Method used
Image
Examples
Embodiment 1
[0033] Prepare a 1:1 volume ratio water and ethanol mixed solution in a 200ml beaker, and heat it to 80°C in a water bath under continuous stirring. Weigh 18.02g magnesium nitrate (Mg(NO 3 ) 2 ·6H 2 O), 52.74g aluminum nitrate (Al(NO 3 ) 3 9H 2 O) or 33.94g aluminum chloride (AlCl 3 ·6H 2 O) and 88.625g citric acid (C 6 h 8 o 7 ·H 2 O) Dissolve in water and ethylene glycol mixed solution to make CA / Mg / Al 6:1:2 to obtain a light yellow transparent sol, and heat it in a water bath to make it a viscous dark red transparent gel. The gel was transferred to an evaporating dish while it was hot, and aged in an oven for 36 hours. Put the evaporating dish into a muffle furnace and ventilate it with air, roast at 450°C for 2 hours to remove citric acid, cool to room temperature and grind evenly, then put it into a muffle furnace and roast at 700°C for 12 hours to obtain a white magnesium aluminum spinel carrier.
Embodiment 2
[0035] Prepare a 1:1 volume ratio water and ethanol mixed solution in a 200ml beaker, and heat it to 80°C in a water bath under continuous stirring. Take by weighing 16.22g magnesium nitrate (Mg(NO 3 ) 2 ·6H 2 O), 47.47g aluminum nitrate (Al(NO 3 ) 3 9H 2 O) or 33.94g aluminum chloride (AlCl 3 ·6H 2 O) and 88.625g citric acid (C 6 h 8 o 7 ·H 2 O) Dissolve in water and ethylene glycol mixed solution to make CA / Mg / Al 6:0.9:2 to obtain a light yellow transparent sol, and heat it in a water bath to make it a viscous deep red transparent gel. The gel was transferred to an evaporating dish while it was hot, and aged in an oven for 36 hours. Put the evaporating dish into a muffle furnace and ventilate it with air, roast at 450°C for 2 hours to remove citric acid, cool to room temperature and grind evenly, then put it into a muffle furnace and roast at 700°C for 12 hours to obtain a white magnesium aluminum spinel carrier.
Embodiment 3
[0037] Prepare a 1:1 volume ratio water and ethanol mixed solution in a 200ml beaker, and heat it to 80°C in a water bath under continuous stirring. Weigh 18.02g magnesium nitrate (Mg(NO 3 ) 2 ·6H 2 O), 58.01g aluminum nitrate (Al(NO 3 ) 3 9H 2 O) or 37.33g aluminum chloride (AlCl 3 ·6H 2 O) and 88.625g citric acid (C 6 h 8 o 7 ·H 2 O) Dissolve in water and ethylene glycol mixed solution to make CA / Mg / Al 6:1:2.2 to obtain a light yellow transparent sol, and heat it in a water bath to make it a viscous dark red transparent gel. The gel was transferred to an evaporating dish while it was hot, and aged in an oven for 36 hours. Put the evaporating dish into a muffle furnace and ventilate it with air, roast at 450°C for 2 hours to remove citric acid, cool to room temperature and grind evenly, then put it into a muffle furnace and roast at 700°C for 12 hours to obtain a white magnesium aluminum spinel carrier.
PUM
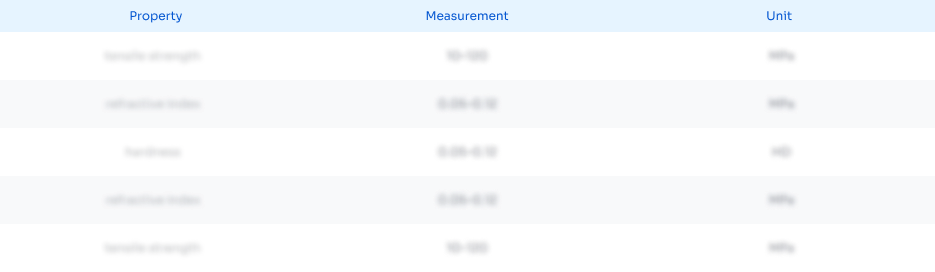
Abstract
Description
Claims
Application Information

- Generate Ideas
- Intellectual Property
- Life Sciences
- Materials
- Tech Scout
- Unparalleled Data Quality
- Higher Quality Content
- 60% Fewer Hallucinations
Browse by: Latest US Patents, China's latest patents, Technical Efficacy Thesaurus, Application Domain, Technology Topic, Popular Technical Reports.
© 2025 PatSnap. All rights reserved.Legal|Privacy policy|Modern Slavery Act Transparency Statement|Sitemap|About US| Contact US: help@patsnap.com