PCB with hollow cavity structure and manufacturing method therefor
The technology of a PCB board and a manufacturing method is applied to the PCB board with a cavity structure and its manufacturing field, which can solve problems such as difficulty and reduce transmission loss, and achieve the effects of simple manufacturing process, reduced loss, and low cost
- Summary
- Abstract
- Description
- Claims
- Application Information
AI Technical Summary
Problems solved by technology
Method used
Image
Examples
Embodiment Construction
[0023] Below, in conjunction with accompanying drawing and specific embodiment, the present invention is described further:
[0024] see figure 1 , the present invention provides a PCB board with a cavity structure, which is a multilayer board, including a first copper clad laminate 1, a second copper clad laminate 2, an adhesive sheet substrate 3 and a differential transmission line 4, the first copper clad laminate 1. The bonding sheet base material 3 and the second copper clad laminate 2 are arranged in sequence from top to bottom. The first copper clad laminate 1 comprises a first light plate 11, the upper end surface and the lower end surface of the first light plate 11 are respectively provided with a first copper clad layer 12; the second copper clad laminate 2 comprises a second light plate 21, the lower surface of the second light plate 21 The end face is provided with the second copper clad layer 22; The upper end surface of the bonding sheet 3 is milled to form a ...
PUM
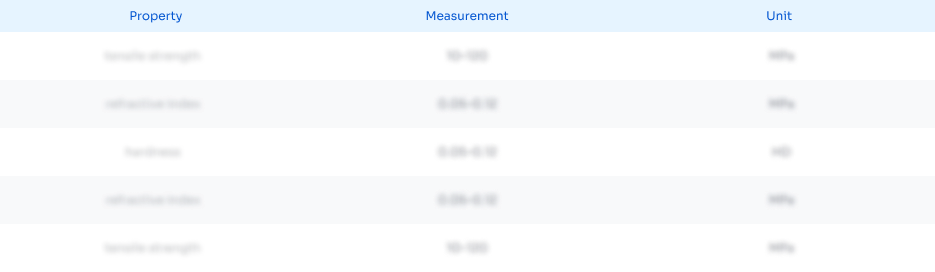
Abstract
Description
Claims
Application Information

- R&D
- Intellectual Property
- Life Sciences
- Materials
- Tech Scout
- Unparalleled Data Quality
- Higher Quality Content
- 60% Fewer Hallucinations
Browse by: Latest US Patents, China's latest patents, Technical Efficacy Thesaurus, Application Domain, Technology Topic, Popular Technical Reports.
© 2025 PatSnap. All rights reserved.Legal|Privacy policy|Modern Slavery Act Transparency Statement|Sitemap|About US| Contact US: help@patsnap.com