Hoisting system for hot pressed sintering mold
A technology of hot pressing sintering and mold, which is applied in the field of machinery, can solve the problems of worker injury, target products, large manpower, etc., and achieve the effects of reducing deformation, improving accuracy and stability, and improving efficiency
- Summary
- Abstract
- Description
- Claims
- Application Information
AI Technical Summary
Problems solved by technology
Method used
Image
Examples
Embodiment Construction
[0059] As mentioned in the background technology, the mold used in the hot-press sintering process has a large mass. For this reason, the raw material powder loading step of the hot-press sintering, the step of placing the hot-press sintering mold into the hot-press sintering furnace, and the step after the hot-press sintering process The demoulding step process is complex, inefficient, and highly dangerous.
[0060] For this reason, the invention provides a hot pressing sintering mold hoisting system.
[0061] The hot pressing sintering mold lifting system includes:
[0062] The casting mold sleeve is used to place the hot-pressed sintering raw materials, and the casting mold sleeve is a cylindrical structure with upper and lower ends open;
[0063] The tray is placed under the casting mold sleeve and closes the opening of the lower end of the casting mold sleeve, and the surface edge of the tray for placing the casting mold sleeve is formed with a plurality of gaps;
[006...
PUM
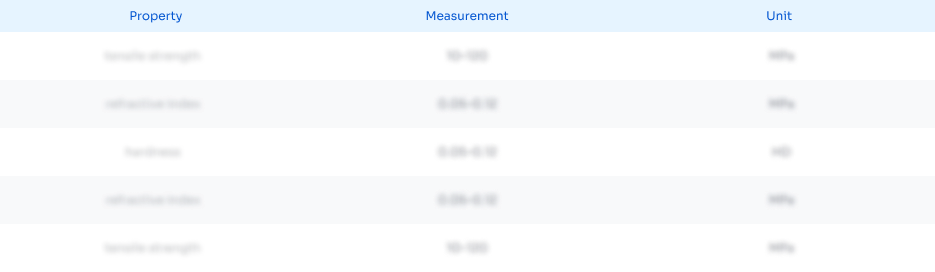
Abstract
Description
Claims
Application Information

- R&D
- Intellectual Property
- Life Sciences
- Materials
- Tech Scout
- Unparalleled Data Quality
- Higher Quality Content
- 60% Fewer Hallucinations
Browse by: Latest US Patents, China's latest patents, Technical Efficacy Thesaurus, Application Domain, Technology Topic, Popular Technical Reports.
© 2025 PatSnap. All rights reserved.Legal|Privacy policy|Modern Slavery Act Transparency Statement|Sitemap|About US| Contact US: help@patsnap.com