Control method and equipment for suturing and centering thin strip steel for continuous annealing furnace
A technology of continuous annealing furnace and control method, which is applied in the field of strip rolling, can solve the problems such as the risk of broken strips of the unit and poor alignment accuracy, and achieve the effects of reducing the risk of broken strips, improving stitching precision, and smooth production
- Summary
- Abstract
- Description
- Claims
- Application Information
AI Technical Summary
Problems solved by technology
Method used
Image
Examples
Embodiment Construction
[0032] The present invention will be described in further detail below in conjunction with the accompanying drawings.
[0033] Such as figure 1 As shown, the control device of the present invention is provided with a first pressure roller at the head of the forward strip, and a second pressure roller is provided at the tail of the trailing strip, and the first pressure roller and the second pressure roller are lifted at ordinary times. When carrying out the centering operation, the first pressure roller and the second pressure roller are pressed down, and the bottom frames of the first pressure roller and the second pressure roller are fixed, and only play the effect of fixing the strip steel.
[0034] A first deviation-correcting roller is arranged at the tail of the forward strip, and a second deviation-correcting roller is arranged at the head of the trailing strip, and the bottom frames of the first deviation-correcting roller and the second deviation-correcting roller are...
PUM
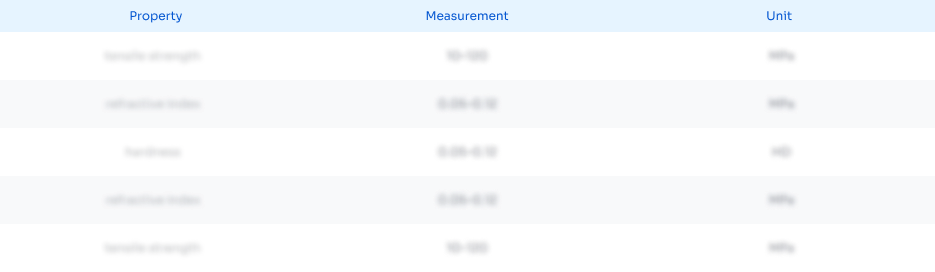
Abstract
Description
Claims
Application Information

- Generate Ideas
- Intellectual Property
- Life Sciences
- Materials
- Tech Scout
- Unparalleled Data Quality
- Higher Quality Content
- 60% Fewer Hallucinations
Browse by: Latest US Patents, China's latest patents, Technical Efficacy Thesaurus, Application Domain, Technology Topic, Popular Technical Reports.
© 2025 PatSnap. All rights reserved.Legal|Privacy policy|Modern Slavery Act Transparency Statement|Sitemap|About US| Contact US: help@patsnap.com