Stretch forming technical method for high-temperature alloy materials
A technology of stretch forming and process method, which is applied in the forming field of superalloy materials, can solve the problems of long forming cycle, unsuitable parts production, cracks, etc., and achieve the effect of improving production efficiency and quality
- Summary
- Abstract
- Description
- Claims
- Application Information
AI Technical Summary
Problems solved by technology
Method used
Examples
Embodiment Construction
[0012] The specific description of the present invention is as follows:
[0013] Step 1: Cut the wool according to the shape of the part;
[0014] Step 2: Stretch the shape of the part on the skin stretching machine. The two ends of the sheet are clamped by the clamps of the stretching machine, and the stretch tire lifted by the worktable is in contact with the sheet to produce uneven plane tensile strain so that the sheet and the stretch tire are bonded together. The existing stretching process is mainly used on aluminum plate materials, and the stretching process is already a mature technology. When this method is applied to superalloy materials, it should be noted that if the shape of the part cannot meet the requirements of stretch forming, it can be segmented from the middle, and then the segmented stretched parts can be welded together. The key to stretching superalloys lies in the structural form of the stretched tire. It is necessary to find an optimal stretching dir...
PUM
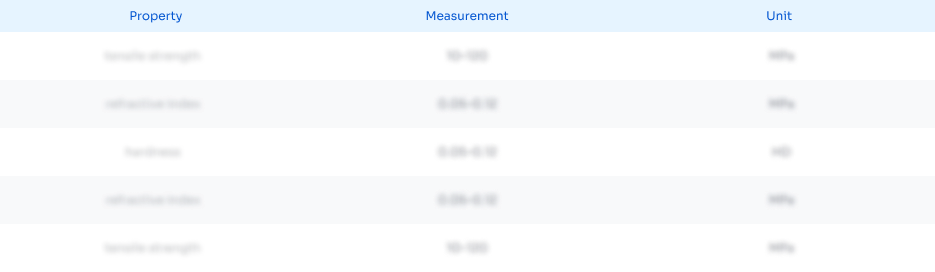
Abstract
Description
Claims
Application Information

- Generate Ideas
- Intellectual Property
- Life Sciences
- Materials
- Tech Scout
- Unparalleled Data Quality
- Higher Quality Content
- 60% Fewer Hallucinations
Browse by: Latest US Patents, China's latest patents, Technical Efficacy Thesaurus, Application Domain, Technology Topic, Popular Technical Reports.
© 2025 PatSnap. All rights reserved.Legal|Privacy policy|Modern Slavery Act Transparency Statement|Sitemap|About US| Contact US: help@patsnap.com