High-precision ultralow frequency six-dimensional force micro-vibration measuring system
A measurement system and micro-vibration technology, applied to measurement devices, ultrasonic/sonic/infrasonic waves, instruments, etc., can solve the problems of inflexible installation interface, low measurement accuracy of micro-vibration measurement system, etc., to improve anti-interference ability and test Accuracy, real-time measurement accuracy improvement, good signal-to-noise ratio effect
- Summary
- Abstract
- Description
- Claims
- Application Information
AI Technical Summary
Problems solved by technology
Method used
Image
Examples
Embodiment Construction
[0035] Further illustrate the present invention below in conjunction with accompanying drawing.
[0036] Such as Figure 1-5 As shown, the high-precision ultra-low frequency six-dimensional force micro-vibration measurement system of the present invention includes a box body 1, a load plate 2, four vertical piezoelectric sensors 3, six horizontal piezoelectric sensors 4, and six lateral positioning plates 5. Signal adjustment device 9 and data acquisition and processing system 10 .
[0037] Wherein, box body 1 is made up of casing 11 and base 12, and casing 11 is the hollow structure of bottom end opening, and the top surface of casing 11 is provided with first central through hole 111, and side is provided with window 112, facilitates casing 1 The internal piezoelectric sensor is routed and when the disturbance source is arranged inside the box body 1, it is convenient to operate the disturbance source; the base 12 is fixed on the bottom opening of the housing 11, and forms ...
PUM
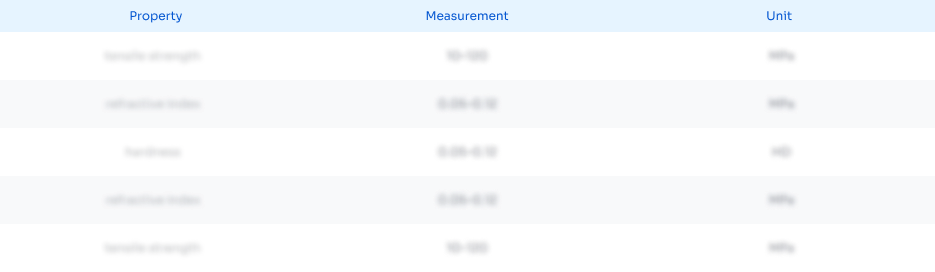
Abstract
Description
Claims
Application Information

- R&D Engineer
- R&D Manager
- IP Professional
- Industry Leading Data Capabilities
- Powerful AI technology
- Patent DNA Extraction
Browse by: Latest US Patents, China's latest patents, Technical Efficacy Thesaurus, Application Domain, Technology Topic, Popular Technical Reports.
© 2024 PatSnap. All rights reserved.Legal|Privacy policy|Modern Slavery Act Transparency Statement|Sitemap|About US| Contact US: help@patsnap.com