A cable automatic exhaust line system
An automatic wire and cable technology, which is applied in the direction of thin material handling, delivery of filamentous materials, transportation and packaging, etc., can solve the problem of not always being able to maintain an ideal position, affecting the stability of the take-up work, and the optical cable running track. Errors and other problems, to achieve the effect of reducing manpower input, simple structure, and stable winding
- Summary
- Abstract
- Description
- Claims
- Application Information
AI Technical Summary
Problems solved by technology
Method used
Image
Examples
Embodiment
[0032] Such as Figure 1-2 As shown, the present embodiment discloses an automatic cable arrangement system, which includes in sequence according to the production process: a wire releasing device 10, a sheath processing device, a cooling device 9, a wire storage device 7, a well frame 2 4, Well frame 1 3, wire device 2 and wire take-up device 1. After the cable core is released from the above-mentioned wire-releasing device 10, it is wrapped with a sheath by the sheath processing device, and then cooled by the above-mentioned cooling device 9, and then enters the above-mentioned wire storage device after cooling 7. Supported by the well-tac-toe frame two 4 and the well-tac-toe frame one 3, then enter the above-mentioned take-up device 1 through the above-mentioned wire device 2.
[0033] Wherein, the above-mentioned well-tac-toe frame one 3 and the well-tac-toe frame two 4 are used to support the cables that are transported, the well-tac-toe frame one 3 is close to the above-...
PUM
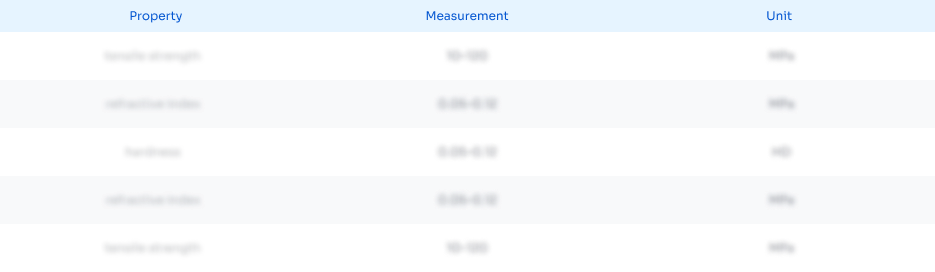
Abstract
Description
Claims
Application Information

- R&D
- Intellectual Property
- Life Sciences
- Materials
- Tech Scout
- Unparalleled Data Quality
- Higher Quality Content
- 60% Fewer Hallucinations
Browse by: Latest US Patents, China's latest patents, Technical Efficacy Thesaurus, Application Domain, Technology Topic, Popular Technical Reports.
© 2025 PatSnap. All rights reserved.Legal|Privacy policy|Modern Slavery Act Transparency Statement|Sitemap|About US| Contact US: help@patsnap.com