PP (Polypropylene) plastic injection molding machine
A technology for injection molding machines and plastics, applied in the field of injection molding machines, can solve problems such as reducing product quality, uneven heating, and screw wear of injection molding machines, and achieves the effects of saving costs and maintenance costs, improving production efficiency, and increasing transmission capacity.
- Summary
- Abstract
- Description
- Claims
- Application Information
AI Technical Summary
Problems solved by technology
Method used
Image
Examples
Embodiment Construction
[0016] The following will clearly and completely describe the technical solutions in the embodiments of the present invention with reference to the accompanying drawings in the embodiments of the present invention. Obviously, the described embodiments are only some, not all, embodiments of the present invention. Based on the embodiments of the present invention, all other embodiments obtained by persons of ordinary skill in the art without making creative efforts belong to the protection scope of the present invention.
[0017] see Figure 1~4 , in an embodiment of the present invention, a PP plastic injection molding machine includes a feeding device, a machine barrel 12, a screw 13, a base 24, a motor 25, a metering device 28 and a machine head 29, and the feeding device includes a mixing bucket 1 and Feed hopper 9, the discharge opening of described mixing bucket 1 is arranged on the feed inlet of feeding hopper 9, and described mixing bucket 1 is inverted conical, and desc...
PUM
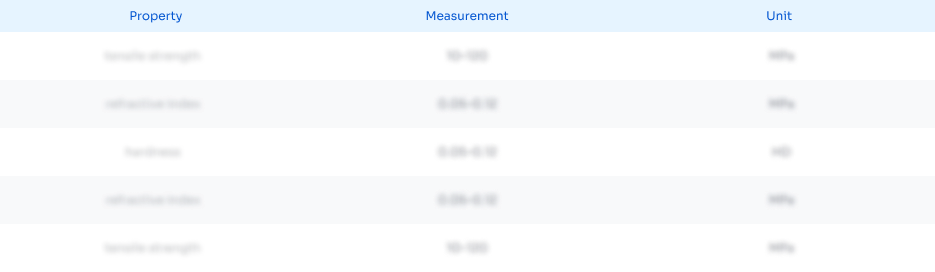
Abstract
Description
Claims
Application Information

- R&D
- Intellectual Property
- Life Sciences
- Materials
- Tech Scout
- Unparalleled Data Quality
- Higher Quality Content
- 60% Fewer Hallucinations
Browse by: Latest US Patents, China's latest patents, Technical Efficacy Thesaurus, Application Domain, Technology Topic, Popular Technical Reports.
© 2025 PatSnap. All rights reserved.Legal|Privacy policy|Modern Slavery Act Transparency Statement|Sitemap|About US| Contact US: help@patsnap.com