Yarn manufacturing mechanism with yarn tension adjusting function
A yarn tension and function technology, applied in the field of yarn making mechanisms with yarn tension adjustment function, can solve the problems of yarn detachment, unbalanced wrapping, low production efficiency, etc., and achieve flexible yarn tension and overall design Reasonable and ensure the effect of product quality
- Summary
- Abstract
- Description
- Claims
- Application Information
AI Technical Summary
Problems solved by technology
Method used
Image
Examples
Embodiment 1
[0025] Such as Figure 1-3 As shown, the yarn making mechanism with yarn tension adjustment function includes a central bobbin 2 through which the central yarn 1 passes, and the central bobbin 2 is fixedly connected with the turntable 3, and the turntable 3 is provided with at least A spindle 4, the mechanism also includes an adjustment plate 7 that is arranged on the spindle 4 and is located in the bobbin 6 that is wound with the yarn 5 on the spindle 4, and the adjustment plate 7 is provided with a number of yarn through holes 8, The yarn passing through holes 8 are distributed on the adjusting plate 7 and the number of the yarn passing through holes 8 to be passed is determined according to the yarns 5 of different materials. The yarn 5 enters the yarn passing hole 8 of the adjusting plate through the spindle 4 from the bobbin 6, and the yarn passing hole 8 has a certain friction force on the yarn. Yarn 5 passes through more yarn passing holes 8, and when yarn 5 needs less...
PUM
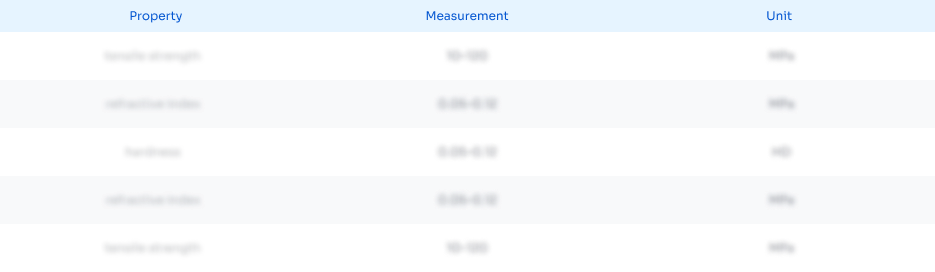
Abstract
Description
Claims
Application Information

- R&D
- Intellectual Property
- Life Sciences
- Materials
- Tech Scout
- Unparalleled Data Quality
- Higher Quality Content
- 60% Fewer Hallucinations
Browse by: Latest US Patents, China's latest patents, Technical Efficacy Thesaurus, Application Domain, Technology Topic, Popular Technical Reports.
© 2025 PatSnap. All rights reserved.Legal|Privacy policy|Modern Slavery Act Transparency Statement|Sitemap|About US| Contact US: help@patsnap.com