Device and method for producing low-dispersion coefficient carbon fibers
A discrete coefficient and carbon fiber technology, applied in the fields of fiber chemical characteristics, textiles and papermaking, etc., can solve problems such as unstable production and unresolved basic scientific problems
- Summary
- Abstract
- Description
- Claims
- Application Information
AI Technical Summary
Problems solved by technology
Method used
Image
Examples
Embodiment 1
[0020] After the polyacrylonitrile precursor is uncoiled, it is pre-treated by a saturated steam device and a drying oven. The steam pressure is 0.15MPa, the residence time is 3min, and the draft ratio is 5%. The drying oven temperature is 120°C, and the drying time is 5 minutes. Then, preoxidation is carried out by gradually increasing the temperature at 180-300°C under air atmosphere, low-temperature carbonization is carried out at 300-800°C under inert gas, and high-temperature carbonization is carried out at 900-1500°C. Finally, the carbon fiber is obtained by winding, the tensile strength of the carbon fiber is 4540MPa, and the dispersion coefficient of the tensile strength is 2.15%; the tensile modulus is 257GPa, and the dispersion coefficient of the tensile modulus is 2.21%.
Embodiment 2
[0022] After the polyacrylonitrile precursor is uncoiled, it is pretreated by a saturated steam device and a drying oven. The steam pressure is 0.2 MPa, the residence time is 3 minutes, and the draft ratio is 5%. The drying oven temperature is 120°C, and the drying time is 5 minutes. Then, preoxidation is carried out by gradually increasing the temperature at 180-300°C under air atmosphere, low-temperature carbonization is carried out at 300-800°C under inert gas, and high-temperature carbonization is carried out at 900-1500°C. Finally, the carbon fiber is obtained by winding. The tensile strength of the carbon fiber is 4670MPa, and the dispersion coefficient of the tensile strength is 2.12%; the tensile modulus is 259GPa, and the dispersion coefficient of the tensile modulus is 2.09%.
Embodiment 3
[0024] After the polyacrylonitrile precursor is uncoiled, it is pre-treated by a saturated steam device and a drying oven. The steam pressure is 0.3MPa, the residence time is 3min, and the draft ratio is 5%. The drying oven temperature is 120°C, and the drying time is 5 minutes. Then, preoxidation is carried out by gradually increasing the temperature at 180-300°C under air atmosphere, low-temperature carbonization is carried out at 300-800°C under inert gas, and high-temperature carbonization is carried out at 900-1500°C. Finally, the carbon fiber is obtained by winding, the tensile strength of the carbon fiber is 4850MPa, and the dispersion coefficient of the tensile strength is 1.98%; the tensile modulus is 264GPa, and the dispersion coefficient of the tensile modulus is 1.89%.
PUM
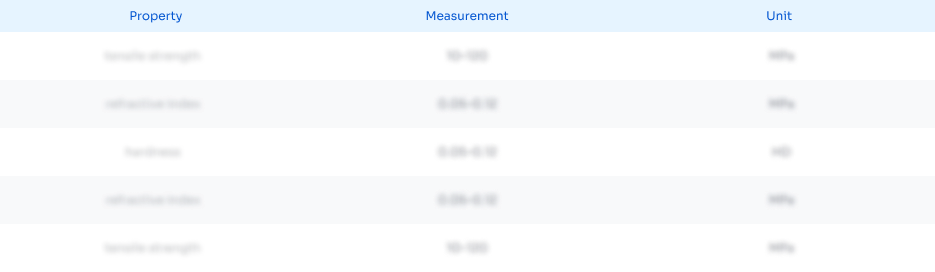
Abstract
Description
Claims
Application Information

- Generate Ideas
- Intellectual Property
- Life Sciences
- Materials
- Tech Scout
- Unparalleled Data Quality
- Higher Quality Content
- 60% Fewer Hallucinations
Browse by: Latest US Patents, China's latest patents, Technical Efficacy Thesaurus, Application Domain, Technology Topic, Popular Technical Reports.
© 2025 PatSnap. All rights reserved.Legal|Privacy policy|Modern Slavery Act Transparency Statement|Sitemap|About US| Contact US: help@patsnap.com