Preparation method of high-performance reverse-osmosis anti-pollution film
A reverse osmosis and anti-pollution technology, applied in reverse osmosis, semi-permeable membrane separation, chemical instruments and methods, etc., can solve problems such as increased system operating costs, poor water quality, and decreased membrane flux, and achieve good water quality. Flux and rejection rate, good anti-pollution performance, low cost of preparation
- Summary
- Abstract
- Description
- Claims
- Application Information
AI Technical Summary
Problems solved by technology
Method used
Examples
Embodiment 1
[0024] Add 0.1% polyethyleneimine to 1% glycerin aqueous solution, mix evenly, and apply it on the reverse osmosis basement membrane. After 20 seconds, pour off the excess solution and dry it in the shade. The aqueous solution of glutaraldehyde was coated on the shade-dried film, and after 30 seconds, the excess solution was poured off, and treated in an oven at 70°C for 2 minutes. The reverse osmosis anti-fouling membrane prepared by this method was continuously operated for 96 hours in a mixture solution with a concentration of sodium chloride of 500 ppm and bovine serum albumin of 1000 ppm. After 96 hours, the water flux and interception were tested, and the water flux was determined to be 60LMH, and the desalination rate was 99.6%.
Embodiment 2
[0026] Add 0.3% polyethyleneimine to 2% glycerin aqueous solution, mix evenly, coat on the reverse osmosis basement membrane, pour off the excess solution after 20s, dry in the shade, and use 0.2% polyvinyl alcohol and 1% The aqueous solution of glutaraldehyde was coated on the shade-dried film, and after 30 seconds, the excess solution was poured off, and treated in an oven at 70°C for 2 minutes. The reverse osmosis anti-fouling membrane prepared by this method was continuously operated for 96 hours in a mixture solution with a concentration of sodium chloride of 500 ppm and bovine serum albumin of 1000 ppm. After 96 hours, the water flux and interception were tested, and the water flux was determined to be 61LMH, and the desalination rate was 99.5%.
Embodiment 3
[0028] Add 0.4% polyethyleneimine to 2% glycerin aqueous solution, mix evenly, and coat it on the reverse osmosis basement membrane. After 20 seconds, pour off the excess solution and dry it in the shade. The aqueous solution of glutaraldehyde was coated on the shade-dried film, and after 30 seconds, the excess solution was poured off, and treated in an oven at 70°C for 2 minutes. The reverse osmosis anti-fouling membrane prepared by this method was continuously operated for 96 hours in a mixture solution with a concentration of sodium chloride of 500 ppm and bovine serum albumin of 1000 ppm. After 96 hours, the water flux and interception were tested, and the water flux was 62LMH, and the desalination rate was 99.6%.
PUM
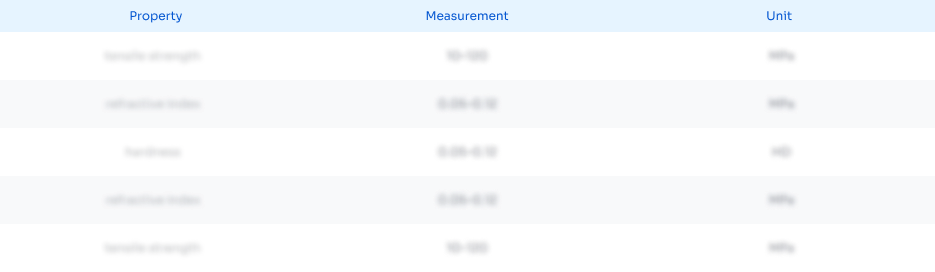
Abstract
Description
Claims
Application Information

- R&D
- Intellectual Property
- Life Sciences
- Materials
- Tech Scout
- Unparalleled Data Quality
- Higher Quality Content
- 60% Fewer Hallucinations
Browse by: Latest US Patents, China's latest patents, Technical Efficacy Thesaurus, Application Domain, Technology Topic, Popular Technical Reports.
© 2025 PatSnap. All rights reserved.Legal|Privacy policy|Modern Slavery Act Transparency Statement|Sitemap|About US| Contact US: help@patsnap.com