Constant current driving system and constant current driving method for stepping motor with fixed duty ratio
A technology of stepping motor and fixed duty, applied in the control system, motor generator control, electrical components, etc., can solve the problems of poor portability and scalability, complex hardware circuit structure, poor software flexibility, etc., to reduce software Hardware design complexity, simplified software design, and the effect of simplified software and hardware design
- Summary
- Abstract
- Description
- Claims
- Application Information
AI Technical Summary
Problems solved by technology
Method used
Image
Examples
Embodiment Construction
[0039] image 3 Shown is the block diagram of the constant current drive structure of the stepper motor of the present invention, a constant current drive system of the stepper motor with a fixed duty ratio of the present invention, including a control unit 1, a drive circuit 2, a power circuit 3, a stepper motor 4, a current Sensor 5, protection circuit 6; Control unit includes pulse divider 7, PWM generator 10 and logic operator 11; The improvement of this system is: control unit also includes comparator 12, and described comparator includes input positive terminal, Input the negative terminal and the output terminal, the input negative terminal is used to input the given value of the motor winding current, the input positive terminal is connected to the current sensor to receive the feedback value of the motor winding current; the output terminal is connected to the logic operator;
[0040] The system uses a comparison unit to replace the A / D conversion and PID solver or hy...
PUM
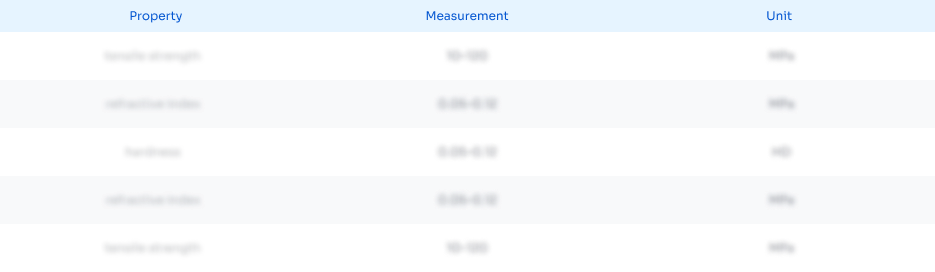
Abstract
Description
Claims
Application Information

- R&D
- Intellectual Property
- Life Sciences
- Materials
- Tech Scout
- Unparalleled Data Quality
- Higher Quality Content
- 60% Fewer Hallucinations
Browse by: Latest US Patents, China's latest patents, Technical Efficacy Thesaurus, Application Domain, Technology Topic, Popular Technical Reports.
© 2025 PatSnap. All rights reserved.Legal|Privacy policy|Modern Slavery Act Transparency Statement|Sitemap|About US| Contact US: help@patsnap.com