No-lens wide-beam parallel light transmitting and receiving system
A technology for transmitting, receiving, and transmitting systems, which is applied in the field of lensless wide-beam parallel light transmitting and receiving systems, can solve the problems of affecting the rotation or swing rate, inaccurate measurement results, and increased lens quality, so as to increase the rotation or swing rate, improve The effects of universal applicability and widened size range
- Summary
- Abstract
- Description
- Claims
- Application Information
AI Technical Summary
Problems solved by technology
Method used
Image
Examples
Embodiment Construction
[0021] In order to better understand the present invention, the present invention will be further described below in conjunction with specific embodiments and accompanying drawings.
[0022] Such as figure 1 As shown, a lensless wide-beam parallel light emitting and receiving system includes a light emitting system and a light receiving system. The light emitting system includes a point light source 1, a cylindrical prism 2 located obliquely below the point light source 1, a The emission plane mirror 3 on the bottom right of the columnar prism 2 and the emission parabolic concave mirror 4 located at the left obliquely below the emission plane mirror 3, and the light receiving system includes a horizontally symmetrical arrangement with the emission parabolic concave mirror 4 A receiving parabolic concave mirror 6, a receiving plane mirror 7 located obliquely above the receiving parabolic concave mirror 6, and a CCD (Charge Coupled Device) array detector 9 located obliquely abov...
PUM
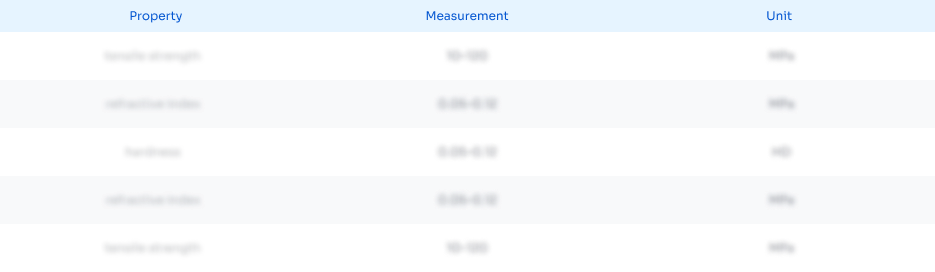
Abstract
Description
Claims
Application Information

- R&D Engineer
- R&D Manager
- IP Professional
- Industry Leading Data Capabilities
- Powerful AI technology
- Patent DNA Extraction
Browse by: Latest US Patents, China's latest patents, Technical Efficacy Thesaurus, Application Domain, Technology Topic, Popular Technical Reports.
© 2024 PatSnap. All rights reserved.Legal|Privacy policy|Modern Slavery Act Transparency Statement|Sitemap|About US| Contact US: help@patsnap.com