A kind of anti-pilling wool surface air layer fabric
An air layer, anti-pilling technology, applied in the direction of wear-resistant fibers, textiles and papermaking, fiber processing, etc., can solve the problems of reducing the friction coefficient of the fiber surface, complex composition of anti-pilling additives, and unfavorable large-scale production, etc. Achieve the effect of increasing warmth retention, simple and easy drying operation, and reducing directional friction effect
- Summary
- Abstract
- Description
- Claims
- Application Information
AI Technical Summary
Problems solved by technology
Method used
Image
Examples
Embodiment 1
[0023] The anti-pilling wool face air layer fabric of embodiment 1, the air layer fabric is formed by sewing the wool fabric and the air layer auxiliary material, and the wool fabric is subjected to anti-pilling finishing, and the above-mentioned anti-pilling finishing includes the following steps:
[0024] S1: Configure the first finishing solution and the second finishing solution. The main components of the first finishing solution are keratin powder, organic acid and water. The weight percentage of keratin powder in the first finishing solution is 1%; The main components are ethylenediamine-modified polylactic acid, ethyl lactate and polycarbodiimide, the weight percentage of ethylenediamine-modified polylactic acid in the second finishing liquid is 0.2%, polycarbodiimide and ethylenediimide The weight ratio of amine-modified polylactic acid is 0.03:1;
[0025] S2: Soak the woolen fabric in the first finishing solution for 1 hour at room temperature, take out the fabric, a...
Embodiment 2
[0030] The difference between embodiment 2 and embodiment 1 is: the weight percent of keratin powder in the first finishing solution is 4%; the weight percent of ethylenediamine-modified polylactic acid in the second finishing solution is 2%, and the The weight ratio of amine to ethylenediamine-modified polylactic acid is 0.1:1; S2: soak the woolen fabric in the first finishing solution, soak it for 3 hours at room temperature, take out the fabric, and heat it to 70°C for drying under vacuum and reduced pressure; S3 : Pad the wool fabric twice in the second finishing solution, take it out, and dry it at a temperature lower than 70°C.
[0031] The weight percentage of the organic acid in the first finishing solution is 70%; the second finishing solution contains a plasticizer tributyl citrate, and the weight ratio of the plasticizer to ethylenediamine-modified polylactic acid is 0.01:1.
Embodiment 3
[0033] The difference between embodiment 3 and embodiment 1 is: the weight percent of keratin powder in the first finishing solution is 2.5%; the weight percent of ethylenediamine-modified polylactic acid in the second finishing solution is 1.1%, polycarbodiimide The weight ratio of amine to ethylenediamine-modified polylactic acid is 0.65:1; S2: soak the wool fabric in the first finishing solution for 2 hours at room temperature, take out the fabric, and heat it to 65°C under vacuum to dry it; S3 : Pad the wool fabric twice in the second finishing solution, take it out, and dry it at a temperature lower than 70°C.
[0034] The weight percentage of the organic acid in the first finishing solution is 80%; the second finishing solution contains a plasticizer, acetyl tributyl citrate, and the weight ratio of the plasticizer to ethylenediamine-modified polylactic acid is 0.02:1.
PUM
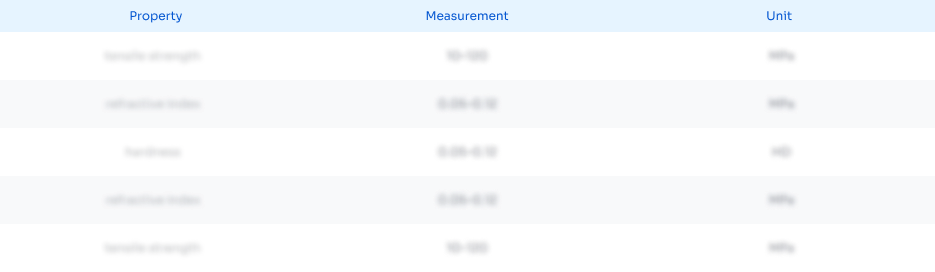
Abstract
Description
Claims
Application Information

- R&D
- Intellectual Property
- Life Sciences
- Materials
- Tech Scout
- Unparalleled Data Quality
- Higher Quality Content
- 60% Fewer Hallucinations
Browse by: Latest US Patents, China's latest patents, Technical Efficacy Thesaurus, Application Domain, Technology Topic, Popular Technical Reports.
© 2025 PatSnap. All rights reserved.Legal|Privacy policy|Modern Slavery Act Transparency Statement|Sitemap|About US| Contact US: help@patsnap.com