Textile fiber oiling device
A fiber and oil drum technology, applied in fiber processing, textiles and papermaking, filament/thread forming, etc., can solve problems such as uneven fiber, affecting fiber performance, and oil not recovered, so as to achieve fiber compactness and good promotion and utilization value effect
- Summary
- Abstract
- Description
- Claims
- Application Information
AI Technical Summary
Problems solved by technology
Method used
Image
Examples
Embodiment Construction
[0017] Embodiment of the present invention is described below in conjunction with accompanying drawing, embodiment does not constitute limitation of the present invention:
[0018] Such as figure 1 , figure 2 As shown, the structure of this kind of textile fiber oiling device includes a working chamber 1, an oil barrel 2 is arranged at the upper left end of the outside of the working chamber 1, and a filter 3 is arranged inside the oil barrel 2. The lower end is provided with a fuel injector 4, and the upper end of the oil drum 2 is provided with an oil suction pump 5. Therefore, when in use, the oil drum 2 can collect recovered emulsified oil through the oil suction pump 5 and reuse it through the filter screen 3. The fuel injector 4. It can atomize the emulsified oil, so that the emulsified oil can be evenly attached to the surface of the fiber.
[0019] In the above example, specifically, the upper right side of the working chamber 1 is provided with an exhaust hole 8, a...
PUM
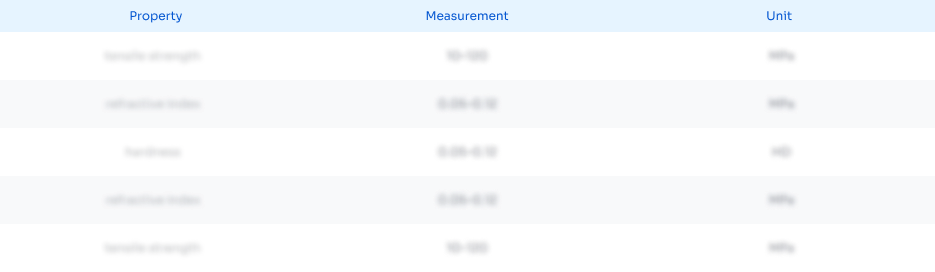
Abstract
Description
Claims
Application Information

- R&D Engineer
- R&D Manager
- IP Professional
- Industry Leading Data Capabilities
- Powerful AI technology
- Patent DNA Extraction
Browse by: Latest US Patents, China's latest patents, Technical Efficacy Thesaurus, Application Domain, Technology Topic, Popular Technical Reports.
© 2024 PatSnap. All rights reserved.Legal|Privacy policy|Modern Slavery Act Transparency Statement|Sitemap|About US| Contact US: help@patsnap.com