Manganese zinc ferrite material for resisting EMI and preparation method thereof
A technology of manganese-zinc ferrite and auxiliary materials, applied in the field of ferrite materials, can solve the problems of insufficient comprehensive properties of materials, low Curie temperature, and insufficient Bs, and achieve high magnetic permeability, high Curie temperature, and comprehensive magnetic properties. Excellent effect
- Summary
- Abstract
- Description
- Claims
- Application Information
AI Technical Summary
Problems solved by technology
Method used
Examples
Embodiment 1
[0026] will be proportioned as Fe 2 o 3 : 51.16mol%, ZnO: 20.1mol%, Mn 3 o 4 : 28.74mol% (converted into mass percentage as Fe 2 o 3 : 68.98wt%, ZnO: 13.81wt%, Mn 3 o 4 : 17.21wt%) of the three main raw materials are mixed, and then pre-fired at a temperature of 700-1000 ° C, by adding the auxiliary component CaCO 3 : 200ppm, Bi 2 o 3 : 300ppm, MoO 3 : 100ppm, TiO 2 : 400ppm, and other auxiliary components Nb 2 o 5 : 75ppm, after mixing, ball milling, drying, granulation, compression molding, molding pressure 8MPa, and finally sintering, the sintering process is: heating to 1100°C at a heating rate of 2-4°C / min, and oxygen in this section The pressure concentration is controlled at 0.05%, and this section is controlled at a very low oxygen partial pressure concentration; then heated to 1350°C at a heating rate of 1-3°C / min, and first kept warm for 8 hours, and the oxygen partial pressure concentration is controlled at 21%. Then keep warm for 4h again, the oxygen p...
Embodiment 2
[0029] will be proportioned as Fe 2 o 3 : 51.44mol%, ZnO: 20.28mol%, Mn 3 o 4 : 28.28mol% of the three main raw materials are mixed, and then pre-fired at a temperature of 700-1000 ° C, by adding the auxiliary component CaCO 3 : 200ppm, Bi 2 o 3 :: 300ppm, MoO 3 : 100ppm, TiO 2 : 400ppm, and other auxiliary components Nb 2 o 5 : 100ppm, mixed by ball milling, drying, granulation, and then compression molding. The sintering process and test conditions are the same as in Example 1. The test results are shown in Table 1 and Table 2.
Embodiment 3
[0031] Under the constant situation of keeping the master formula of embodiment 1, suitably adjust the MoO in the minor formula 3 Increased to 350ppm, Nb 2 o 5 reduced to 50ppm and TiO 2 Reduced to 250ppm, after mixing, ball milling, drying, granulation, then compression molding, sintering with the same sintering process as in Example 1. The results can still achieve the target. When the frequency is ≤200kHz, the magnetic permeability increases, but when it exceeds 200kHz, the magnetic permeability decreases faster, and the impedance coefficient decreases. The test results are shown in Table 1 and Table 2.
PUM
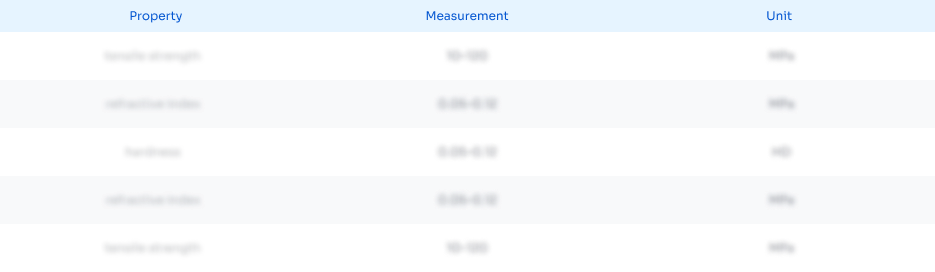
Abstract
Description
Claims
Application Information

- R&D Engineer
- R&D Manager
- IP Professional
- Industry Leading Data Capabilities
- Powerful AI technology
- Patent DNA Extraction
Browse by: Latest US Patents, China's latest patents, Technical Efficacy Thesaurus, Application Domain, Technology Topic, Popular Technical Reports.
© 2024 PatSnap. All rights reserved.Legal|Privacy policy|Modern Slavery Act Transparency Statement|Sitemap|About US| Contact US: help@patsnap.com