Robot intelligent tooling system
A robot intelligence and robot technology, applied in the field of manufacturing engineering, can solve the problems that combined tooling is difficult to meet the high-efficiency and high-precision machining, design, manufacture, drive, and control of aircraft thin-walled curved surface parts, and it is difficult to meet the actual needs of aerospace vehicles, etc. , to achieve the effect of simplified daily maintenance, strong scalability, and reduced application costs
- Summary
- Abstract
- Description
- Claims
- Application Information
AI Technical Summary
Problems solved by technology
Method used
Image
Examples
Embodiment Construction
[0031] In order to achieve the above purpose, the invention figure 1 The robot intelligent tooling system shown (hereinafter referred to as the tooling system). The system controls the coordinated movement of the dual robots through a computer to realize the intelligent operation of the tooling system. The whole system includes a base part 5, a moving beam part 3, a saddle part 4, a telescopic unit 2, a universal vacuum suction head 1, a left robot 7, a right robot 8, a control computer 9 and other components. It is characterized in that: the base part 5 is equipped with a plurality of moving beam parts 3, and each moving beam part moves along the X coordinate; the moving beam part is equipped with a plurality of sliding saddle parts 4, and each sliding saddle part moves along the Y coordinate; A telescopic unit 2 is installed on the saddle part, and the telescopic unit drives the universal vacuum suction head 1 at its top to move along the Z coordinate. Wherein, the Z coord...
PUM
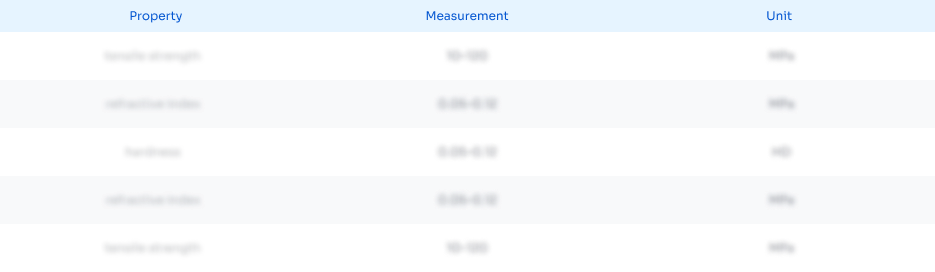
Abstract
Description
Claims
Application Information

- R&D
- Intellectual Property
- Life Sciences
- Materials
- Tech Scout
- Unparalleled Data Quality
- Higher Quality Content
- 60% Fewer Hallucinations
Browse by: Latest US Patents, China's latest patents, Technical Efficacy Thesaurus, Application Domain, Technology Topic, Popular Technical Reports.
© 2025 PatSnap. All rights reserved.Legal|Privacy policy|Modern Slavery Act Transparency Statement|Sitemap|About US| Contact US: help@patsnap.com