A kind of preparation method of sodium niobate ceramic material with stable antiferroelectricity and low dielectric loss
A technology of antiferroelectricity and ceramic materials is applied in the field of preparation of sodium niobate ceramic materials, which can solve the problem of failing to obtain stable antiferroelectricity, and achieve the effects of reducing material cost, simplifying complexity, and alleviating volatilization.
- Summary
- Abstract
- Description
- Claims
- Application Information
AI Technical Summary
Problems solved by technology
Method used
Image
Examples
Embodiment 1
[0031] The ball milling conditions are as follows: the ball-to-material ratio is 15:1, the ball milling speed is 1000 / min, and the ball milling time is 90 minutes. The NaNbO prepared by high-energy ball milling 3 Without adding any binder, the powder is molded directly under the pressure of 800MPa, with a diameter of 11.5mm and a thickness of about 1.5mm; then the rate of 7°C / min increases from room temperature to 650°C, and then 3.4°C / min The rate of min is raised to 950°C, and then the rate of 4°C / min is raised to 1350°C for buried powder sintering, and the temperature is kept for 2 hours to obtain the target ceramic material.
Embodiment 2
[0033] The ball milling conditions are as follows: the ball-to-material ratio is 20:1, the ball milling speed is 800 / min, and the ball milling time is 90 minutes. The NaNbO prepared by high-energy ball milling 3 Without adding any binder, the powder is molded directly under the pressure of 800MPa, with a diameter of 11.5mm and a thickness of about 1.5mm; then the rate of 7°C / min increases from room temperature to 650°C, and then 3.4°C / min The rate of min is raised to 950°C, and then the rate of 4°C / min is raised to 1365°C for buried powder sintering, and the temperature is kept for 2 hours to obtain the target ceramic material. From Figure 5 and 6 It can be seen that there is a new dielectric peak around T=100°C, which has never been reported in the existing literature of sodium niobate. The appearance of this abnormal dielectric peak indicates that there is a stable antiferroelectric phase at room temperature, and the electrical test shows that the beam waist double hyster...
Embodiment 3
[0035] The ball milling conditions are: the ball-to-material ratio is 30:1, the ball milling speed is 600 / min, and the ball milling time is 120min. The NaNbO prepared by high-energy ball milling 3 Without adding any binder, the powder is directly molded under the pressure of 800MPa, with a diameter of 11.5mm and a thickness of about 1.5mm; then the rate of 7°C / min increases from room temperature to 650°C, 3.4°C / min The speed is increased to 950°C, and then the speed is increased to 1375°C at a rate of 4°C / min for powder sintering, and the temperature is kept for 2 hours to obtain the target ceramic material.
PUM
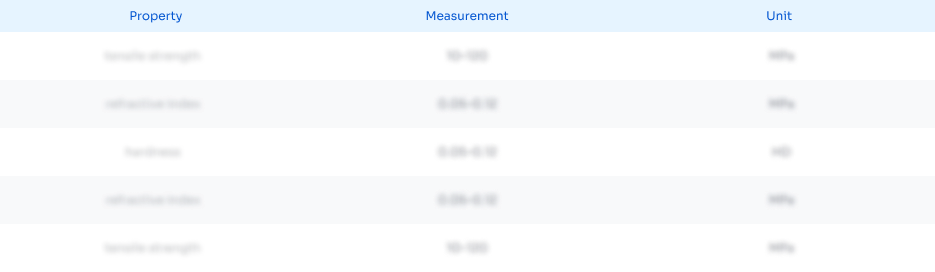
Abstract
Description
Claims
Application Information

- R&D
- Intellectual Property
- Life Sciences
- Materials
- Tech Scout
- Unparalleled Data Quality
- Higher Quality Content
- 60% Fewer Hallucinations
Browse by: Latest US Patents, China's latest patents, Technical Efficacy Thesaurus, Application Domain, Technology Topic, Popular Technical Reports.
© 2025 PatSnap. All rights reserved.Legal|Privacy policy|Modern Slavery Act Transparency Statement|Sitemap|About US| Contact US: help@patsnap.com