Hypersonic speed aircraft skin cooling and semiconductor thermoelectric power generation integrated system
A hypersonic, thermoelectric power generation technology, applied in the directions of generators/motors, electrical components, etc., can solve the problems of aircraft surface thermal protection aircraft power supply, etc., and achieve the effect of lowering temperature, lowering quality and high reliability
- Summary
- Abstract
- Description
- Claims
- Application Information
AI Technical Summary
Problems solved by technology
Method used
Image
Examples
specific Embodiment approach 1
[0015] Specific implementation mode 1: Combination figure 1 To illustrate this embodiment, the hypersonic aircraft skin cooling and semiconductor thermoelectric power generation integrated system described in this embodiment includes a skin 1, a semiconductor thermoelectric power generation module 9, two thermally conductive insulating layers 4, a fuel channel 6 and a Root wire 7;
[0016] The semiconductor thermoelectric power generation module 9 is fixed between two thermally conductive insulating layers 4, one side of the skin 1 is fixed on the outside of a thermally conductive insulating layer 4, the other side of the skin 1 is the heat flow 10; the fuel channel 6 is fixed on one side On the outside of the other thermally conductive insulating layer 4; the fuel channel 10 is used to circulate lower temperature fuel;
[0017] The semiconductor thermoelectric power generation module 9 is composed of M P-type semiconductor thermoelectric materials 2, M N-type semiconductor thermo...
specific Embodiment approach 2
[0023] Embodiment 2: This embodiment further defines the hypersonic aircraft skin cooling and semiconductor thermoelectric power generation integrated system described in Embodiment 1. In this embodiment, M P-type semiconductor thermoelectric materials 2 and M The N-type semiconductor thermoelectric materials 3 are all made of lead telluride. Lead telluride is a polar compound, which is a typical semiconductor. It has significant infrared photoconductivity and is a good thermoelectric material.
specific Embodiment approach 3
[0024] Specific embodiment three: This embodiment further defines the hypersonic aircraft skin cooling and semiconductor thermoelectric power integrated system described in the second embodiment. In this embodiment, M P-type semiconductor thermoelectric materials 2 and M The operating temperature range of the N-type semiconductor thermoelectric material 3 is 300°C-600°C.
PUM
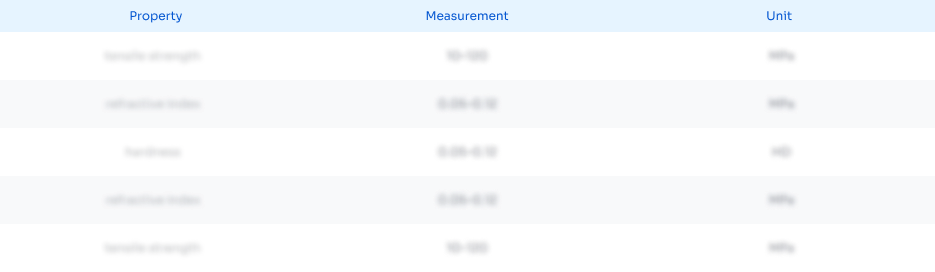
Abstract
Description
Claims
Application Information

- R&D
- Intellectual Property
- Life Sciences
- Materials
- Tech Scout
- Unparalleled Data Quality
- Higher Quality Content
- 60% Fewer Hallucinations
Browse by: Latest US Patents, China's latest patents, Technical Efficacy Thesaurus, Application Domain, Technology Topic, Popular Technical Reports.
© 2025 PatSnap. All rights reserved.Legal|Privacy policy|Modern Slavery Act Transparency Statement|Sitemap|About US| Contact US: help@patsnap.com