Method for reducing calcium content of vacuum residue and processing method of vacuum residue
A technology for vacuum residual oil and calcium content, which is applied in hydrotreating process, multi-stage series refining process treatment, petroleum industry, etc. It can solve the problems of increased cost and insignificant decrease in calcium content of residual oil, etc., and achieves operation The effect of short cycle, low cost and high reaction temperature
- Summary
- Abstract
- Description
- Claims
- Application Information
AI Technical Summary
Problems solved by technology
Method used
Examples
Embodiment 1
[0081] This example is used to illustrate the method for reducing the calcium content in the vacuum residue and the processing method for the vacuum residue of the present invention.
[0082] The properties of vacuum residue with high calcium content are shown in Table 1 below.
[0083] (1) Solvent deasphalting treatment of vacuum residue with high calcium content: the solvent is n-heptane, the extraction temperature is 230°C, the operating pressure is 3MPa, and the volume ratio of solvent to vacuum residue is 8:1. After extraction, the yield of DAVR relative to the vacuum residue raw material is 89.3% by weight, the content of n-heptane insolubles in DAVR is 0.25% by weight, the density is 0.975g / mL, the calcium content is 48μg / g, and the nickel content is 34.6μg / g, the vanadium content is 18.8μg / g.
[0084] (2) Decalcification of heavy oil: fully mix the DAVR obtained in step (1) with catalytic cracking heavy diesel oil, catalytic cracking cycle oil, catalytic cracking oil...
Embodiment 2
[0113] This example is used to illustrate the method for reducing the calcium content in the vacuum residue and the processing method for the vacuum residue of the present invention.
[0114] The vacuum residue with high calcium content used as raw material oil in this embodiment is the same as that in Embodiment 1.
[0115] (1) Solvent deasphalting treatment of vacuum residue with high calcium content: the solvent is n-heptane, the extraction temperature is 250°C, the operating pressure is 3MPa, and the volume ratio of solvent to vacuum residue is 10:1. After extraction, the yield of DAVR relative to the vacuum residue raw material is 85.5% by weight, the content of n-heptane insolubles in DAVR is 0.12% by weight, the density is 0.969g / mL, the calcium content is 41μg / g, and the nickel content is 28.2μg / g, the vanadium content is 13.8μg / g.
[0116] (2) Decalcification of heavy oil: fully mix the DAVR obtained in step (1) with catalytic cracking heavy diesel oil, catalytic cr...
Embodiment 3
[0121] This example is used to illustrate the method for reducing the calcium content in the vacuum residue and the processing method for the vacuum residue of the present invention.
[0122] The vacuum residue with high calcium content used as the feedstock oil in this example is the same as that in Example 1.
[0123] (1) Solvent deasphalting treatment of vacuum residue with high calcium content: the type of solvent, operating conditions and methods are the same as those in Example 1. DAVR properties are the same as in Example 1.
[0124] (2) Decalcification of heavy oil: fully mix the DAVR obtained in step (1) with catalytic cracking heavy diesel oil, catalytic cracking cycle oil and second-line wax oil to obtain heavy oil, and DAVR, catalytic cracking heavy diesel oil, and catalytic cracking cycle The weight ratio of oil and second-line wax oil is 65:18:9:8, and the density of heavy oil after mixing is 0.94g / mL.
[0125] Decalcifying agent, demulsifier kind and consumpti...
PUM
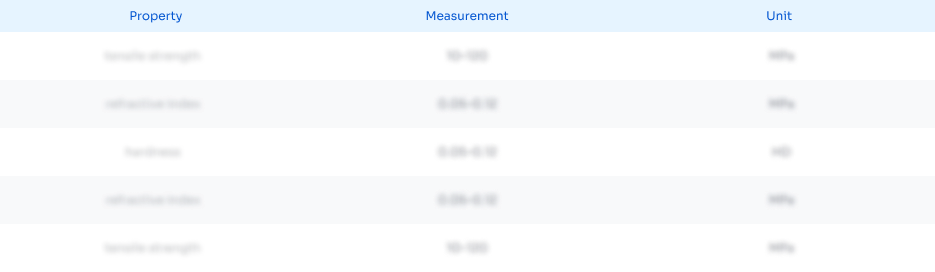
Abstract
Description
Claims
Application Information

- R&D
- Intellectual Property
- Life Sciences
- Materials
- Tech Scout
- Unparalleled Data Quality
- Higher Quality Content
- 60% Fewer Hallucinations
Browse by: Latest US Patents, China's latest patents, Technical Efficacy Thesaurus, Application Domain, Technology Topic, Popular Technical Reports.
© 2025 PatSnap. All rights reserved.Legal|Privacy policy|Modern Slavery Act Transparency Statement|Sitemap|About US| Contact US: help@patsnap.com