Steel-structure super-thin intumescent fire-retardant coating and preparing method thereof
An intumescent technology for fire-resistant coatings, applied in the direction of fire-resistant coatings, coatings, etc., can solve problems affecting human health, toxicity, and complex formulas, and achieve low cost, low density, and simple process flow
- Summary
- Abstract
- Description
- Claims
- Application Information
AI Technical Summary
Problems solved by technology
Method used
Image
Examples
Embodiment 1
[0043] Example 1 The ultra-thin intumescent fireproof coating for steel structures is prepared from the following main raw materials (20 kg per part): 17 parts of ammonium polyphosphate, 10 parts of melamine, 6 parts of pentaerythritol, 6 parts of vinyl acetate-ethylene copolymer emulsion, 4 parts of thermoplastic acrylic resin, 5 parts of polyvinyl chloride resin, 3 parts of light calcium carbonate, 2.5 parts of methyl cellulose, 18 parts of deionized water, 1 part of thickener, 3.5 parts of dispersant, 0.1 part of defoamer.
[0044] The preparation steps of ultra-thin intumescent fireproof coating for steel structure are as follows:
[0045] (1) Put the light calcium carbonate in an ultrafine pulverizer, grind it mechanically for 20 minutes, take it out, pour it into a mixer, add thermoplastic acrylic resin, stir (stirring speed is 140r / min) for 20 minutes, and heat to 45°C. Insulation treatment for 40 minutes;
[0046] (2) Put ammonium polyphosphate, melamine and pentaeryt...
Embodiment 2
[0051] Example 2 The ultra-thin intumescent fireproof coating for steel structures is prepared from the following main raw materials (10 kg per part): 20 parts of ammonium polyphosphate, 15 parts of melamine, 10 parts of pentaerythritol, 12 parts of vinyl acetate-ethylene copolymer emulsion, 8 parts of thermoplastic acrylic resin, 10 parts of polyvinyl chloride resin, 7 parts of light calcium carbonate, 3.5 parts of methyl cellulose, 26 parts of deionized water, 2 parts of thickener, 5.0 parts of dispersant, and 0.3 parts of defoamer.
[0052] The preparation steps of ultra-thin intumescent fireproof coating for steel structure are as follows:
[0053] (1) Put the light calcium carbonate in an ultrafine pulverizer, grind it mechanically for 30 minutes, take it out, pour it into a mixer, add thermoplastic acrylic resin, stir (stirring speed is 180r / min) for 30 minutes, heat to 50°C, Insulation treatment for 50 minutes;
[0054] (2) Put ammonium polyphosphate, melamine and pent...
Embodiment 3
[0059] Example 3 The ultra-thin intumescent fireproof coating for steel structures is prepared from the following main raw materials (15 kg per part): 18 parts of ammonium polyphosphate, 12 parts of melamine, 7 parts of pentaerythritol, 8 parts of vinyl acetate-ethylene copolymer emulsion, 5 parts of thermoplastic acrylic resin, 7 parts of polyvinyl chloride resin, 4 parts of light calcium carbonate, 2.8 parts of methyl cellulose, 21 parts of deionized water, 1.3 parts of thickener, 4.0 parts of dispersant, and 0.15 parts of defoamer.
[0060] The preparation steps of ultra-thin intumescent fireproof coating for steel structure are as follows:
[0061] (1) Put the light calcium carbonate in an ultrafine pulverizer, grind it mechanically for 23 minutes, take it out, pour it into a mixer, add thermoplastic acrylic resin, stir (stirring speed is 150r / min) for 23 minutes, heat to 47°C, Insulation treatment for 43 minutes;
[0062] (2) Put the ammonium polyphosphate, melamine and ...
PUM
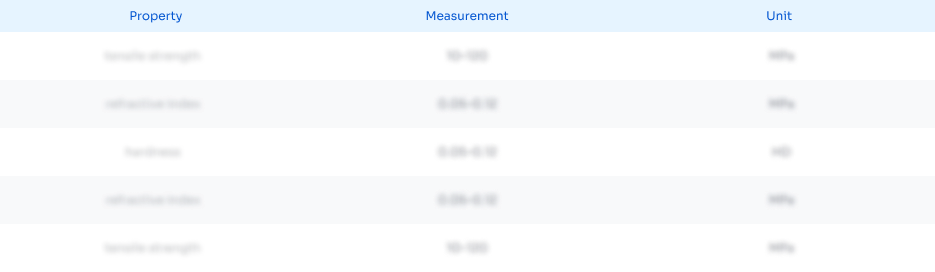
Abstract
Description
Claims
Application Information

- R&D Engineer
- R&D Manager
- IP Professional
- Industry Leading Data Capabilities
- Powerful AI technology
- Patent DNA Extraction
Browse by: Latest US Patents, China's latest patents, Technical Efficacy Thesaurus, Application Domain, Technology Topic, Popular Technical Reports.
© 2024 PatSnap. All rights reserved.Legal|Privacy policy|Modern Slavery Act Transparency Statement|Sitemap|About US| Contact US: help@patsnap.com