Novel disperse print thickening agent and preparation method thereof
A thickener and dispersion technology, applied in the field of textile printing, can solve the problems of low salt resistance and difficult to use alone, and achieve the effects of excellent fastness, bright color and remarkable thickening effect
- Summary
- Abstract
- Description
- Claims
- Application Information
AI Technical Summary
Problems solved by technology
Method used
Examples
Embodiment 1
[0026] Dispersed printing thickener, comprising the following components by weight: 5 parts of hydroxymethyl cellulose; 2 parts of sucrose fatty acid ester; 5 parts of unsaturated acidic monomer; 3 parts of long-chain fatty alcohol polyoxyethylene ether acrylate ; 8 parts of polyacrylic acid; 1 part of sodium 3-prop-2-enoyloxypropane-1-sulfonate; 3 parts of butylene diacrylate; 1 part of diethylene glycol diacrylate; 1 part of initiator; 2 parts of thickening powder; 2 parts of phase inversion agent; 10 parts of deionized water.
Embodiment 2
[0028] Dispersed printing thickener, comprising the following components by weight: 8 parts of hydroxymethyl cellulose; 5 parts of sucrose fatty acid ester; 14 parts of unsaturated acidic monomer; 4 parts of long-chain fatty alcohol polyoxyethylene ether acrylate ; 10 parts of polyacrylic acid; 1.5 parts of sodium 3-prop-2-enoyloxypropane-1-sulfonate; 4 parts of butylene diacrylate; 5 parts of diethylene glycol diacrylate; 3 parts of initiator; inorganic 8 parts of thickening powder; 3 parts of phase inversion agent; 15 parts of deionized water.
Embodiment 3
[0030] Dispersed printing thickener, comprising the following components by weight: 10 parts of hydroxymethyl cellulose; 8 parts of sucrose fatty acid ester; 20 parts of unsaturated acidic monomer; 5 parts of long-chain fatty alcohol polyoxyethylene ether acrylate ; 20 parts of polypropylene; 2 parts of sodium 3-prop-2-enoyloxypropane-1-sulfonate; 8 parts of butylene diacrylate; 8 parts of diethylene glycol diacrylate; 5 parts of initiator; inorganic 15 parts of thickening powder; 5 parts of phase inversion agent; 20 parts of deionized water.
PUM
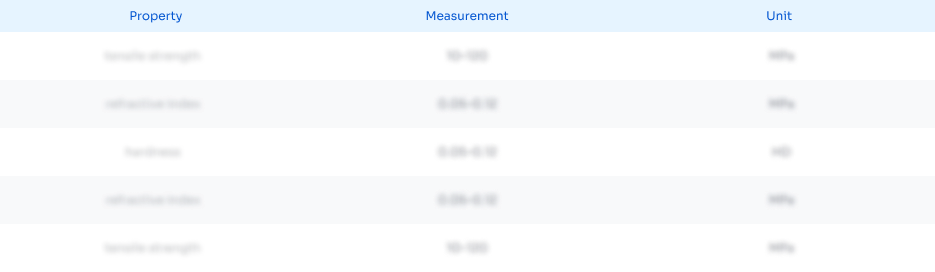
Abstract
Description
Claims
Application Information

- R&D
- Intellectual Property
- Life Sciences
- Materials
- Tech Scout
- Unparalleled Data Quality
- Higher Quality Content
- 60% Fewer Hallucinations
Browse by: Latest US Patents, China's latest patents, Technical Efficacy Thesaurus, Application Domain, Technology Topic, Popular Technical Reports.
© 2025 PatSnap. All rights reserved.Legal|Privacy policy|Modern Slavery Act Transparency Statement|Sitemap|About US| Contact US: help@patsnap.com