Low-smoke halogen-free high-strength polyolefin cable material and preparing method
A polyolefin cable material, high-strength technology, applied in the direction of circuits, electrical components, plastic/resin/wax insulators, etc., can solve problems such as threatening the health of fire victims, hindering rescue work, limiting service life and safety, etc., to achieve Good mechanical and physical properties, outstanding mechanical properties and long service life
- Summary
- Abstract
- Description
- Claims
- Application Information
AI Technical Summary
Problems solved by technology
Method used
Image
Examples
Embodiment 1
[0025] (1) Weighing: Weigh 10 parts of the basic flame retardant with the ratio of calcium hydroxide: aluminum hydroxide: antimony trioxide = 4:2:1, and the synergistic flame retardant with silicone: zinc borate: pentaerythritol = Weigh 6 parts at a ratio of 1:1:1, blend them in a high-speed mixer at 1800r / min for 10 minutes, and put the evenly mixed composite flame retardant in a constant temperature oven at 120°C to dry for 36 hours;
[0026] (2) Modification of composite basic flame retardant: put 10 parts of dry composite basic flame retardant, 3 parts of silane coupling agent, and 6 parts of absolute ethanol into a special reaction kettle, ultrasonically treat for 4 hours, and wait for the ethanol to volatilize Completely, take out the modified composite basic flame retardant and put it in a constant temperature oven at 110°C to dry for 36 hours, and set aside;
[0027] (3) Modification of composite synergistic flame retardant: Put 6 parts of dry composite synergistic fla...
Embodiment 2
[0033] (1) Weighing: The basic flame retardant is weighed in the ratio of calcium hydroxide: aluminum hydroxide: antimony trioxide = 4:2:1, and the synergistic flame retardant is silicone: zinc borate: pentaerythritol = Weigh 8 parts at a ratio of 1:1:1, blend them in a high-speed mixer at 1800r / min for 10 minutes, and put the evenly mixed composite flame retardant in a constant temperature oven at 120°C to dry for 36 hours;
[0034] (2) Modification of composite basic flame retardant: put 15 parts of dry composite basic flame retardant, 2 parts of silane coupling agent, and 6 parts of absolute ethanol into a special reaction kettle, ultrasonically treat for 4 hours, and wait for the ethanol to volatilize Completely, take out the modified composite basic flame retardant and put it in a constant temperature oven at 110°C to dry for 36 hours, and set aside;
[0035] (3) Modification of composite synergistic flame retardant: put 8 parts of dry composite synergistic flame retardan...
Embodiment 3
[0041] (1) Weighing: Weigh 20 parts of the basic flame retardant with the ratio of calcium hydroxide: aluminum hydroxide: antimony trioxide = 4:2:1, and the synergistic flame retardant with silicone: zinc borate: pentaerythritol = Weigh 10 parts at a ratio of 1:1:1, blend them in a high-speed mixer at 1800r / min for 10 minutes, and put the evenly mixed composite flame retardant in a constant temperature oven at 120°C to dry for 36 hours;
[0042] (2) Modification of composite basic flame retardant: put 20 parts of dry composite basic flame retardant, 2 parts of silane coupling agent, and 6 parts of absolute ethanol into a special reaction kettle, ultrasonically treat for 4 hours, and wait for the ethanol to volatilize Completely, take out the modified composite basic flame retardant and put it in a constant temperature oven at 110°C to dry for 36 hours, and set aside;
[0043] (3) Modification of composite synergistic flame retardant: Put 10 parts of dry composite synergistic f...
PUM
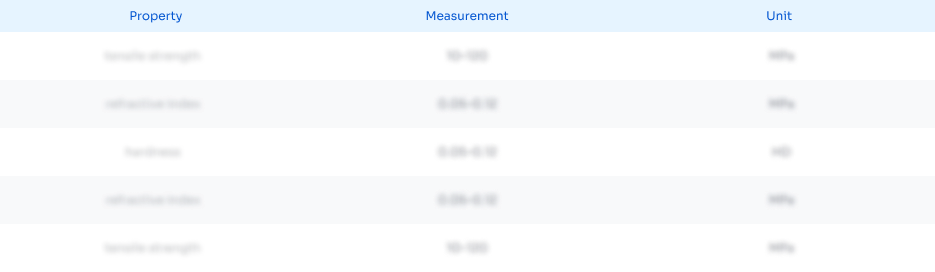
Abstract
Description
Claims
Application Information

- R&D
- Intellectual Property
- Life Sciences
- Materials
- Tech Scout
- Unparalleled Data Quality
- Higher Quality Content
- 60% Fewer Hallucinations
Browse by: Latest US Patents, China's latest patents, Technical Efficacy Thesaurus, Application Domain, Technology Topic, Popular Technical Reports.
© 2025 PatSnap. All rights reserved.Legal|Privacy policy|Modern Slavery Act Transparency Statement|Sitemap|About US| Contact US: help@patsnap.com