Preparation method of low-molecular-weight halogen flame-retardant polycarbonate
A flame retardant polycarbonate, low molecular weight technology, applied in the chemical industry, can solve the problems of difficult synthesis of halogen flame retardant polycarbonate, wide molecular weight distribution, low product qualification rate, etc., and achieves narrow molecular weight distribution, simple operation process, Efficient effect
- Summary
- Abstract
- Description
- Claims
- Application Information
AI Technical Summary
Problems solved by technology
Method used
Examples
Embodiment 1
[0020] Example 1: In a six-necked flask with an electric stirrer, add 100 g of polyhalogenated bisphenol A, 200 g of water, and 530 g of dichloromethane as a solvent, dissolve completely with sodium hydroxide solution under stirring conditions, and add 0.73 g of catalyst triethylamine , the temperature of the system was controlled at 10°C, 33g of phosgene was introduced, and at the same time, the pH of the mixed system was adjusted between 7 and 14 with sodium hydroxide solution, and the prepolymerization reaction time was 20 minutes. After the prepolymerization reaction, increase the reaction temperature to 18°C, add 1.37g of p-tert-butylphenol as an end-capping agent, and add sodium hydroxide solution dropwise at the same time, keep the pH of the system at 7-14, and stir for 30 minutes; After layering, the oil phase was washed three times with process water and hydrochloric acid solution respectively, then the oil phase was added to the precipitant, the white solid was washed...
Embodiment 2
[0021] Example 2: In a six-necked flask with an electric stirrer, add 100 g of polyhalogenated bisphenol A, 250 g of water, and 460 g of dichloromethane as a solvent, dissolve completely with sodium hydroxide solution under stirring conditions, and add 0.5 g of catalyst triethylamine , the temperature of the system was controlled at 11° C., 35 g of phosgene was introduced, and at the same time, the pH of the mixed system was adjusted between 7 and 14 with sodium hydroxide solution, and the prepolymerization reaction time was 15 minutes. After the prepolymerization reaction, raise the reaction temperature to 20°C, add 0.86g of phenol as an end-capping agent, and dropwise add sodium hydroxide solution at the same time to keep the pH of the system at 7-14, and stir for 30 minutes; After the phases were washed three times with process water and hydrochloric acid solution, the oil phase was added to the precipitant, the white solid was washed out, filtered and dried, and a halogen f...
Embodiment 3
[0022] Example 3: In a six-necked flask with an electric stirrer, add polyhalogenated bisphenol A100g, water 300g, solvent methylene chloride 400g, dissolve completely with sodium hydroxide solution under stirring conditions, add catalyst triethylamine 1g, The temperature of the system was controlled at 12°C, 30 g of phosgene was introduced, and at the same time, the pH of the mixed system was adjusted between 7 and 14 with sodium hydroxide solution, and the prepolymerization reaction time was 20 minutes. After the prepolymerization reaction, raise the reaction temperature to 16°C, add 0.86g of phenol as an end-capping agent, and dropwise add sodium hydroxide solution at the same time to keep the pH of the system at 7-14, and stir for 20 minutes; After the phases were washed three times with process water and hydrochloric acid solution, the oil phase was added to the precipitant, the white solid was washed out, filtered and dried, and a halogen flame-retardant polymer with a nu...
PUM
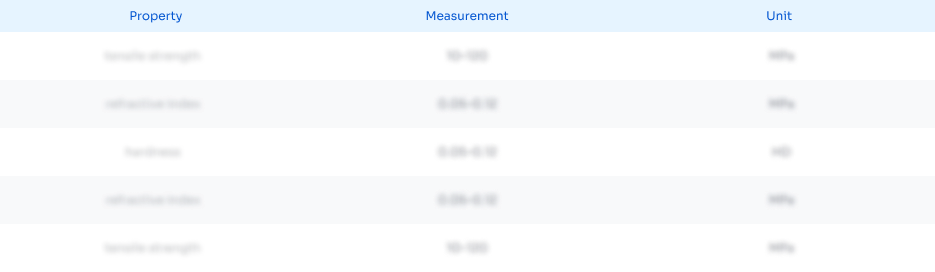
Abstract
Description
Claims
Application Information

- R&D Engineer
- R&D Manager
- IP Professional
- Industry Leading Data Capabilities
- Powerful AI technology
- Patent DNA Extraction
Browse by: Latest US Patents, China's latest patents, Technical Efficacy Thesaurus, Application Domain, Technology Topic, Popular Technical Reports.
© 2024 PatSnap. All rights reserved.Legal|Privacy policy|Modern Slavery Act Transparency Statement|Sitemap|About US| Contact US: help@patsnap.com