Fibrous-composite-wound pressure container with thin-walled metal lining and manufacturing process thereof
A fiber composite material and pressure vessel technology, applied in the field of pressure vessels, can solve the problems of pressure vessel leakage, interface debonding failure, pressure vessel weight increase, etc., to increase the allowable load, fully seal, and avoid local stress. concentrated effect
- Summary
- Abstract
- Description
- Claims
- Application Information
AI Technical Summary
Problems solved by technology
Method used
Image
Examples
Embodiment Construction
[0031] In order to make the purpose, technical solutions and advantages of the embodiments of the present invention clearer, the technical solutions in the embodiments of the present invention will be clearly and completely described below in conjunction with the drawings in the embodiments of the present invention. Obviously, the described embodiments It is a part of embodiments of the present invention, but not all embodiments. Based on the embodiments of the present invention, all other embodiments obtained by persons of ordinary skill in the art without making creative efforts belong to the protection scope of the present invention.
[0032] Such as Figure 1-Figure 3 The thin-walled metal-lined fiber composite wound pressure vessel shown in the first embodiment includes a liner 1 , an elastic material filling layer 2 , a fiber composite wound layer 3 and a medium inlet and outlet (not shown).
[0033] The inner liner 1 includes a thin-walled metal tubular structure inner...
PUM
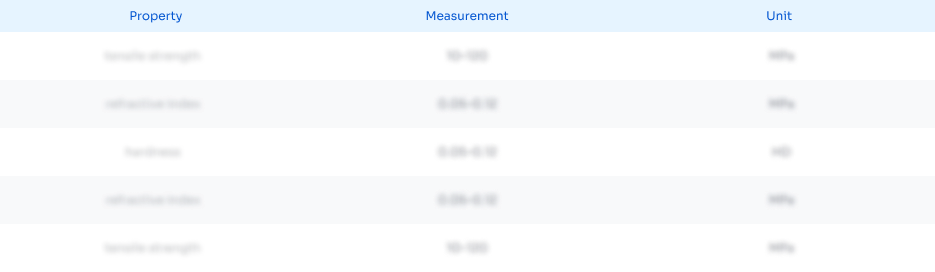
Abstract
Description
Claims
Application Information

- Generate Ideas
- Intellectual Property
- Life Sciences
- Materials
- Tech Scout
- Unparalleled Data Quality
- Higher Quality Content
- 60% Fewer Hallucinations
Browse by: Latest US Patents, China's latest patents, Technical Efficacy Thesaurus, Application Domain, Technology Topic, Popular Technical Reports.
© 2025 PatSnap. All rights reserved.Legal|Privacy policy|Modern Slavery Act Transparency Statement|Sitemap|About US| Contact US: help@patsnap.com