Roller grinding and grinding method of main drive grinding roller friction drive grinding disc
A technology of friction transmission and main transmission, which is applied in the powder preparation, metallurgy, and mining fields of the building materials industry. It can solve the problems of difficulty in manufacturing special reducers and motors, increase the energy consumption of the grinding system, and increase manufacturing costs. Effects of safe operation rate, height reduction, and operating cost reduction
- Summary
- Abstract
- Description
- Claims
- Application Information
AI Technical Summary
Problems solved by technology
Method used
Image
Examples
Embodiment Construction
[0026] The following will clearly and completely describe the technical solutions in the embodiments of the present invention with reference to the accompanying drawings in the embodiments of the present invention. Obviously, the described embodiments are only some, not all, embodiments of the present invention. Based on the embodiments of the present invention, all other embodiments obtained by persons of ordinary skill in the art without creative efforts fall within the protection scope of the present invention.
[0027] Such as figure 1 As shown, the roller mill of the grinding roller friction transmission grinding disc includes: a grinding roller device 28, a grinding roller transmission device 1, a universal coupling 2, a pressurizing device 21, a hinge support device 23, a deflection stop device 25, and a grinding disc 14 , disc liner 13, disc supporting device 18;
[0028] The roller grinding device includes: a roller shaft 3, a roller sleeve 8, a pressurized bearing g...
PUM
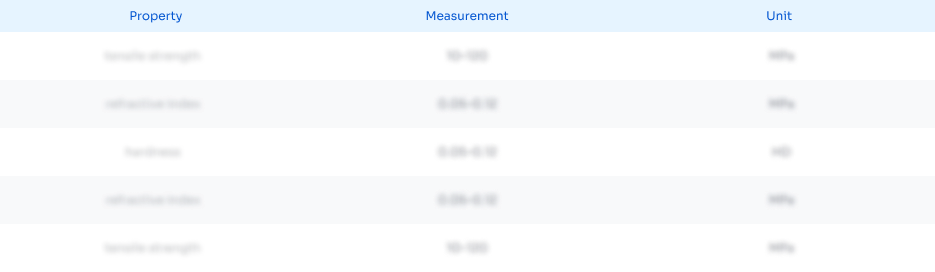
Abstract
Description
Claims
Application Information

- R&D
- Intellectual Property
- Life Sciences
- Materials
- Tech Scout
- Unparalleled Data Quality
- Higher Quality Content
- 60% Fewer Hallucinations
Browse by: Latest US Patents, China's latest patents, Technical Efficacy Thesaurus, Application Domain, Technology Topic, Popular Technical Reports.
© 2025 PatSnap. All rights reserved.Legal|Privacy policy|Modern Slavery Act Transparency Statement|Sitemap|About US| Contact US: help@patsnap.com