Solid waste two-stage pyrolysis gasification system based on fluidized bed and moving bed
A solid waste, pyrolysis gasification technology, applied in gasification process, granular/powdered fuel gasification, combustible gas production, etc., to achieve good solid-solid contact, uniform heating, and high thermal efficiency
- Summary
- Abstract
- Description
- Claims
- Application Information
AI Technical Summary
Problems solved by technology
Method used
Image
Examples
Embodiment 1
[0027] See figure 1, the system includes a solid waste feed system 1 , a pyrolyzer 2 , a biochar collector 3 , a circulating fluidized bed gasifier 4 , a gasifier cyclone separator and a cyclone separation reactor 5 connected in sequence. The solid waste feeding system 1 includes a conveyor 11 and a feeding downcomer 12 , the conveyor 11 communicates with the middle and upper part of the feeding downcomer 12 , and can transport solid waste into the feeding downcomer 12 . The feed downcomer 12 is located above the pyrolyzer 2, and its top is a supplementary bed material inlet 13. The feed downcomer 12 extends deep into the interior of the pyrolyzer 2 until it is above the screw, and there is a certain distance between the screw and the screw. . The material in the feed downcomer 12 provides a material seal.
[0028] The pyrolyzer 2 comprises a pyrolyzer shell, which has a horizontal screw reactor 21 inside and a microwave heater 22 outside. The top of the tail of the pyrolyze...
Embodiment 2
[0034] See figure 2 , The difference between this embodiment and Embodiment 1 is: the feed downcomer is a lock hopper system. The feeding downpipe 12 is a two-section pipe structure with upper and lower sections. A valve is respectively installed at the bottom of the two sections of pipe. The two valves are alternately opened and closed to ensure the sealing of the reaction system and to realize continuous feeding. The bottom of the secondary cyclone separator 7 of the gasifier is respectively connected to the discharge pipe at the lower end of the cyclone separation reactor 5 and the primary cyclone separator 6 of the gasifier. Other system components are the same as in Embodiment 1.
Embodiment 3
[0036] The difference between this embodiment and embodiment 1 is: the cyclone separation reactor 5 is arranged inside the pyrolyzer 2; the screw material of the pyrolyzer 2 is ceramic. Other system components are the same as in Embodiment 1.
PUM
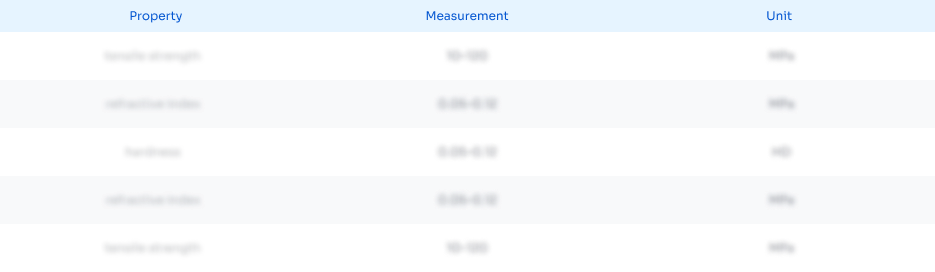
Abstract
Description
Claims
Application Information

- R&D Engineer
- R&D Manager
- IP Professional
- Industry Leading Data Capabilities
- Powerful AI technology
- Patent DNA Extraction
Browse by: Latest US Patents, China's latest patents, Technical Efficacy Thesaurus, Application Domain, Technology Topic, Popular Technical Reports.
© 2024 PatSnap. All rights reserved.Legal|Privacy policy|Modern Slavery Act Transparency Statement|Sitemap|About US| Contact US: help@patsnap.com